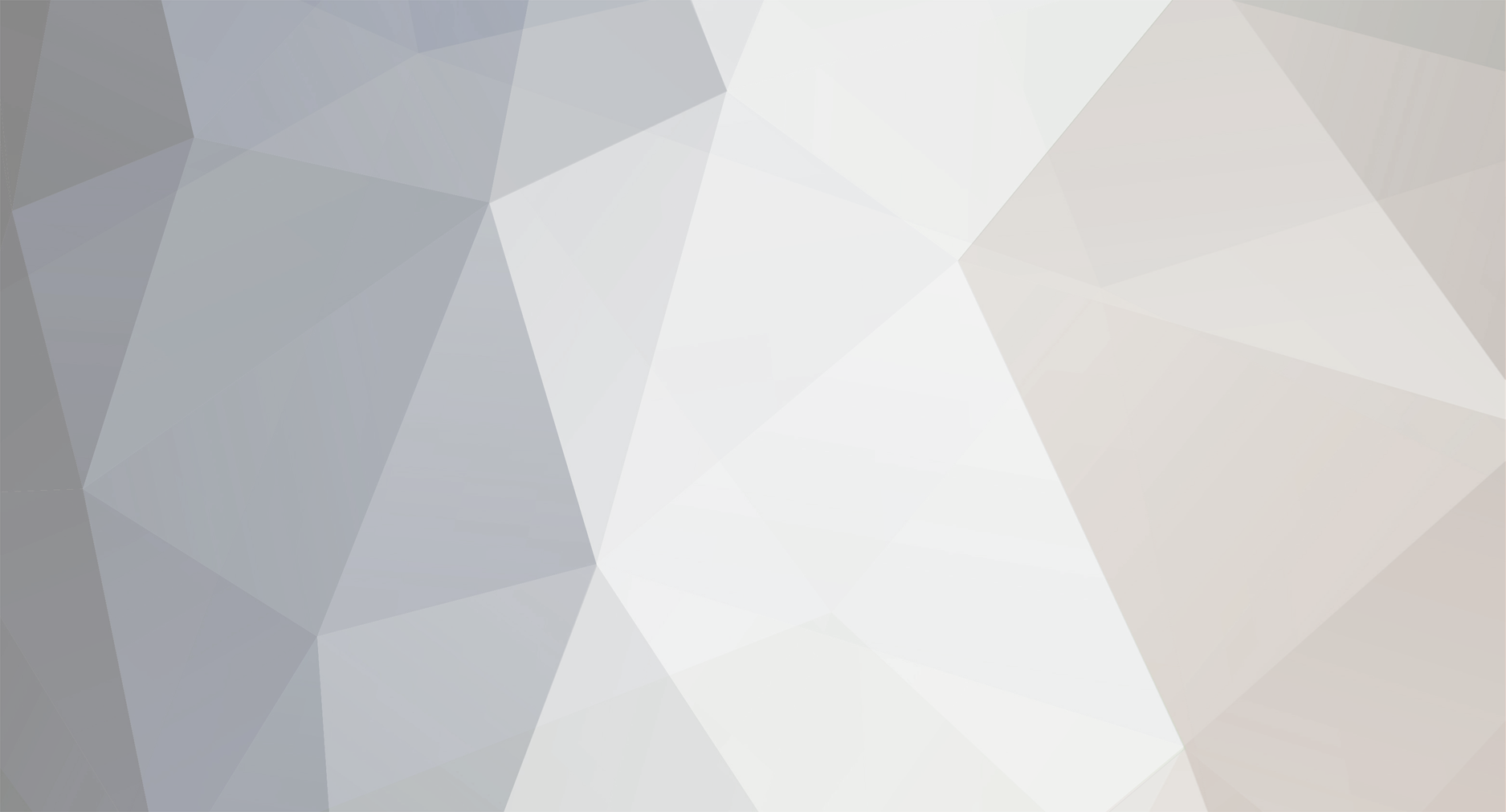
David Holman
Members-
Posts
4,218 -
Joined
-
Last visited
-
Days Won
115
Content Type
Profiles
Forums
Resource Library
Events
Gallery
Blogs
Store
Community Map
Everything posted by David Holman
-
CIE Laminate Coaches - Worsley Works - ECMbuild in 4mm
David Holman replied to murrayec's topic in Irish Models
Lovely stuff. There is so much we can learn here. Note to self: next time I build a coach, check out Eoin's clever jigs and other building aids! -
7mm scale 101 - a tribute to Richard Chown
David Holman replied to David Holman's topic in Workbench
So, where was I? Is it really four weeks since my last post on the 101? An exhibition, man flu [far worse than bubonic plague of course], household chores and the like - they all eat into modelling time! However, as might be gathered from other posts, work has progressed on the 101's tender and the model has now reached the stage where it is not far off the paint shop. The tender, like the loco, proved interesting, to say the least. Frames were straightforward, with 5mm brass rod used for spacers, drilled to take 8BA bolts to fix to the body. At first, this was easy too, the only awkward bit being forming the flares along the top edge. The etches contain a fair amount of detail, including the distinctive tool boxes, plus all the brake gear too. Here is where it started getting complicated, with pull rods both inside and outside the wheels. The real difficulties arose in trying to work out what the original, 1864 gallon, tenders were like on top and at the front. The instructions and photos are of the preserved version, while pictures in books rarely show more than three quarter views of the whole loco, so you are left having to guess what is going on elsewhere. The etches do not cover the tender top surfaces, while [to me at least], it was hard to make sense of the coal space. In the end, I fabricated both from thin brass sheet and it seems ok, while all photos show the tender top liberally covered with coal, so what is underneath hardly matters. Having bemoaned the number of handrails on the loco [eight around the cab alone], I then found there are a further four on the tender. The GSW certainly didn't want its crews falling off the footplate, it seems. As with the loco though, there are no castings in the kit, so I had to source things like springs, axle boxes, buffers etc. I managed to find some suitable spring/axlebox castings at the Reading trade show in December. A fair bit of fettling has been required - separating spring from 'box and filing the latter so they fit in the outside frames. The springs themselves then needed hangers so they can sit on the top edge of the footplate. The etches contain plenty of hangers, but they are flat, so I soldered short lengths of 1mm brass wire to each 'leg' and then rounded this all with a file. This has meant I could drill holes in the footplate surface to take each of the 12 legs. The springs themselves will be glued in place with 5 minute epoxy, probably after painting, because otherwise lining the tender will be difficult. Several things can't be finished until I've visited the Roxy stand at the Tonbridge show next Saturday. A couple of short handrail knobs for the smokebox, a set of etched numbers for the number plates and some sub-miniature plugs and sockets so I can add pick ups to the tender. Hopefully, everything will be ready for priming by then, though this phase can be quite fraught at times. Witness coats do have a habit of showing up unwanted blemishes that then need filling and priming again, while cleaning up always seems to find a few weak solder/glue joints that need doing again. Getting there though. Life is complicated - that's why it is fun. Allegedly... -
Keep 'em coming, Warb. There is much to learn and enjoy here.
-
My 101 is nearing the paint shop stage and livery for the early 1900s is stated as " black, with vermilion lining, edged in white". So, my question is, does that mean a white line either side of the red one, or just one side? And if so, which side - top or bottom? It is very hard to tell from contemporary monochrome photos. Also, can I get away with a wider white line that has a red line down the middle, or were there spaces between the white and red? 7 mm scale remember, so such things are potentially more noticeable.
-
Fabulous. Now that really guilds the lily.
-
A few windows and doors needed too, methinks! Presumably, will be standard size and mass/custom made?
-
I did! Thanks Jonathan. Looked in the 101 loco section and forgot all about the tenders bit. Making progress and will post some pictures next week, but what I will say is that the 101s had a ridiculous number of handrails. 8 just around the cab with four more at the front of the tender.
-
Excellent! Proof, if needed, that printed card works just as well as embossed plastic for buildings. The layers of detail lift the flat surfaces and show what could be done with Metcalfe kits (many of attractive subjects) to cover the exposed corners. Always nice to see individual, scratch built models and this one is a beauty.
-
Many thanks, folks. Key info from Mayner that raves/extensions were not fitted in GSWR days, so a 'flat top' it will be - with a good layer of coal all over. Two cracking photos as well.
-
Well worth a detour if it is at a show in your area. Captures the atmosphere of the prototype beautifully, especially now the village street back scene is nearing completion. 21mm gauge too, which makes it all the better. Prototype modelling at its best! Courtmacsherry is also worthy of study as what must be close to the perfect branchlike setting - regardless of prototype/gauge/company. Sea wall in the foreground, quayside siding, village street as the back scene and the loco shed [or the school] are conveniently place to hide the hole in the sky to the fiddle yard. Why the track plan hasn't been copied much [indeed, at all?] is a real mystery.
-
For what it's worth, I bought a copy of Michael Bunch's Donegal Railway Diary, Part one, at the weekend. Must admit that, initially, I was very disappointed, because the quality of the photos is poor. Overall, I would say close to 50% are grainy, or simply out of focus, while another 25% are poorly composed. However, I'm now warming a little to the book, because if nothing else, it is a unique archive of hard to find views of the more obscure elements of the CDR. It also contains a wealth of generic details, such as platform clutter, piles of parcels, line side and track details, close ups of wagons and coaches, etc. It is just a shame that so many of the pictures are poorly composed/exposed/focussed. Sift through though and there are some real gems, while the price at 15 euros is pretty cheap for an A4 album of 148 pages.
-
Many thanks, these are a lot clearer than anything I have and should make sense of the instructions
-
Instructions on my TMD kit seem a little vague, while those for the front end, particularly the coal shovelling platform refer to the preserved example. Meanwhile, photos in Steaming Through Three Centuries show a fair bit of variety! Am hoping to built the tender as first made in 1902 (Coey loco). So... 1. Would it have had the raves, or would it have been low sided? 2. Presumably, there would have been a front coal sheet, at right angles to the sides, but was there a rear sheet as well? Photos seem to show coal piled full length of the tender top, including round the tank filler. So, a simple flat top to the tender, but with the usual chute down to the front of the tender? 3. Just how is the front coal chute arranged? Instructions suggest a 'coal chute cover ( that you have to make yourself), which will extend down to footplate level and the bottom of this cover is a lifting door.' Any idea what this looks like? As ever, any help much appreciated. Photo shows what is supplied on the etches, but nothing fixed in place yet.
-
Sows' ears being turned into silk purses. we
-
Sounds great, Phil. Keep us posted!
-
Arigna Town - this week's scenery
David Holman replied to David Holman's topic in Irish Model Layouts
Not writing its obituary yet, Andy! That said, the layout almost met a sticky end yesterday afternoon. A little boy, being held up by his grandma, suddenly started coughing, then wailing loudly. Two seconds later, he was spectacularly sick all over her. Poor granny! However, had he turned his head the other way... Anyway, the final day went well enough & everything is back home. As for the future, their are two plans: Plan A To refurbish the layout, to the extent that it may not be instantly recognisable. This is because, I want to turn it around so that the back scene is the other side, thereby changing the view entirely. Apart from the station, all the buildings along the back will be removed, with some, along with the trees, being donated to the Chatham club 0 gauge layout. This is because the layout will be reborn as Belmullet, or more probably 'Black Sod Bay' in the far north west of County Mayo. Jonathan Beaumont, of this parish, covers all the proposals in his book on the Achill Island railway - such things being very must grist to the mill for me in terms of layout ideas. Further changes will involve replacing the turnout to the goods siding with a single slip, enabling an on scene junction to a harbour branch - off scene, of course. In addition, I'm planning a loco shed, beyond the turntable and a back scene which includes a view across Black Sod Bay to the peninsula beyond. All pretty barren and treeless, but shades of Burtonport, which has long been a favourite location too. For an extra twist, I want to turn the clock back to the early 1900s. I have Richard Chown's WLW 'Shannon' and his kit of the 101 class will be in GSW livery of the same period. Add in the MGW's 4-4-0 'Wolf Dog', one of the Sligo small tanks and some new, period stock and there is the makings of a colourful and interesting scene, in addition to the 1950s currently portrayed. I know, all rather unlikely, but I already have a bit of made up history to mind, while all four companies actually met up in Sligo, of course. Plan B I have considered selling Arigna Town as a going concern, with some, but by no means all of the locos and rolling stock. No point in offering the layout on its own, as, apart from Richard Chown's stuff, nobody else appears to do Irish broad gauge in 7mm scale. Was thinking in terms of one of the small tanks, the G class diesel & maybe the J26 and railcar, plus a selection of SLNCR wagons and coaches. However, clearly it wouldn't be cheap - though not as expensive as you might think, but it has been robustly built and is still in very good condition. However, note that this is not a ready to run train set. Everything is hand built and requires a degree of skill to maintain it. Loco servicing, soldering skills should a point tie bar break, etc. In addition, the controls are all at the rear, so to run it at home, a perspective buyer would be looking at adding point and signal motors - which is what I will be doing when/if I refurbish it. Alternatively, while the layout has been widely exhibited in the south of England, it hasn't been seen much at all in the north. If it was sold, then I have another idea for something brand new, but am not thinking about that at the moment. Anyone interested needs to send me a personal message, by the end of February at the latest, so we can discuss what might be available. As a guide, think at least £3-5000, depending on the amount of stock. For now though, here are a selection of photos taken on its final outing. -
Arigna Town - this week's scenery
David Holman replied to David Holman's topic in Irish Model Layouts
One more day. Managed to take some more photos, which will upload tomorrow. Offer new angles that I couldn't do with the layout in the workshop. This evening, have looked back through my journals to create a few statistics on the layout: It is been on the exhibition circuit for four and a half years, racking up 39 shows in all. This equates to over 70 days, or at least 500 hours on display. I reckon that means at least 600 sequences, so each train has travelled about 3000 metres in that time, while the layout itself has done over 10 000 km in the back of my car, plus one return trip from Holyhead to Dublin. Not bad, though am sure there are plenty of layouts that have done far more. Certainly puts exhibiting in perspective though. -
Arigna Town - this week's scenery
David Holman replied to David Holman's topic in Irish Model Layouts
One last outing for Arigna Town this weekend at the Longfield show in Kent. My new layout, Fintonagh, already has five shows booked this year, so the broad gauge will be taking a back seat for a while. Various plans in mind as to what I'm going to do next, so will update you after Longfield. -
CIE Laminate Coaches - Worsley Works - ECMbuild in 4mm
David Holman replied to murrayec's topic in Irish Models
Beautiful. Reminder to self to visit this section more often! -
A fine piece of work, Ken. Highlights too the issues with 3D printing. At a meeting last night, was looking at a 7mm scale open wagon, done complete. From three feet away, it looked impressive, but any closer and the layered effect soon became apparent. Likewise a printed coach, where not sure any amount of sanding and polishing would give a smooth surface and retain the panelling. Apparently, the wagon took six hours to print and many days to get the CAD right. Fine if you enjoy that sort of thing, but not for me just yet, not least because I can produce masters for resin castings in a few hours and once the moulds are set, churn out sides and ends every half hour or so. While I'm here, total respect for the outside cylinder work. I've done St Mologa in 7mm scale, using the Tyrconnel kit. Small engines and outside cylinders make for fag paper clearances around the cross heads. Add in broad gauge and it gets tighter still. Like you, had to move the cylinders out slightly, plus bore the piston rod holes slightly off centre to make it fit. Pretty engine though, so worth the effort.
-
As well as the signature pieces such as the Google building, what makes this layout stand out is the way ordinary, mundane buildings come together so well. Chocolate box cover it ain't, but that's what makes it so special.
-
Try Google search for Lisduff Quarry. Some useful info and pics
-
Am sure you can fit low wattage, 'background' heaters to improve the temperature on an overall basis, Tony. Alternatively, something a bit stronger, but on a timer switch, to come on an hour before you visit, maybe?
-
Interesting to see what the rest of the layout looks like. If it ends up as good as the coastal section, then it will be quite something.
-
Another one to follow!