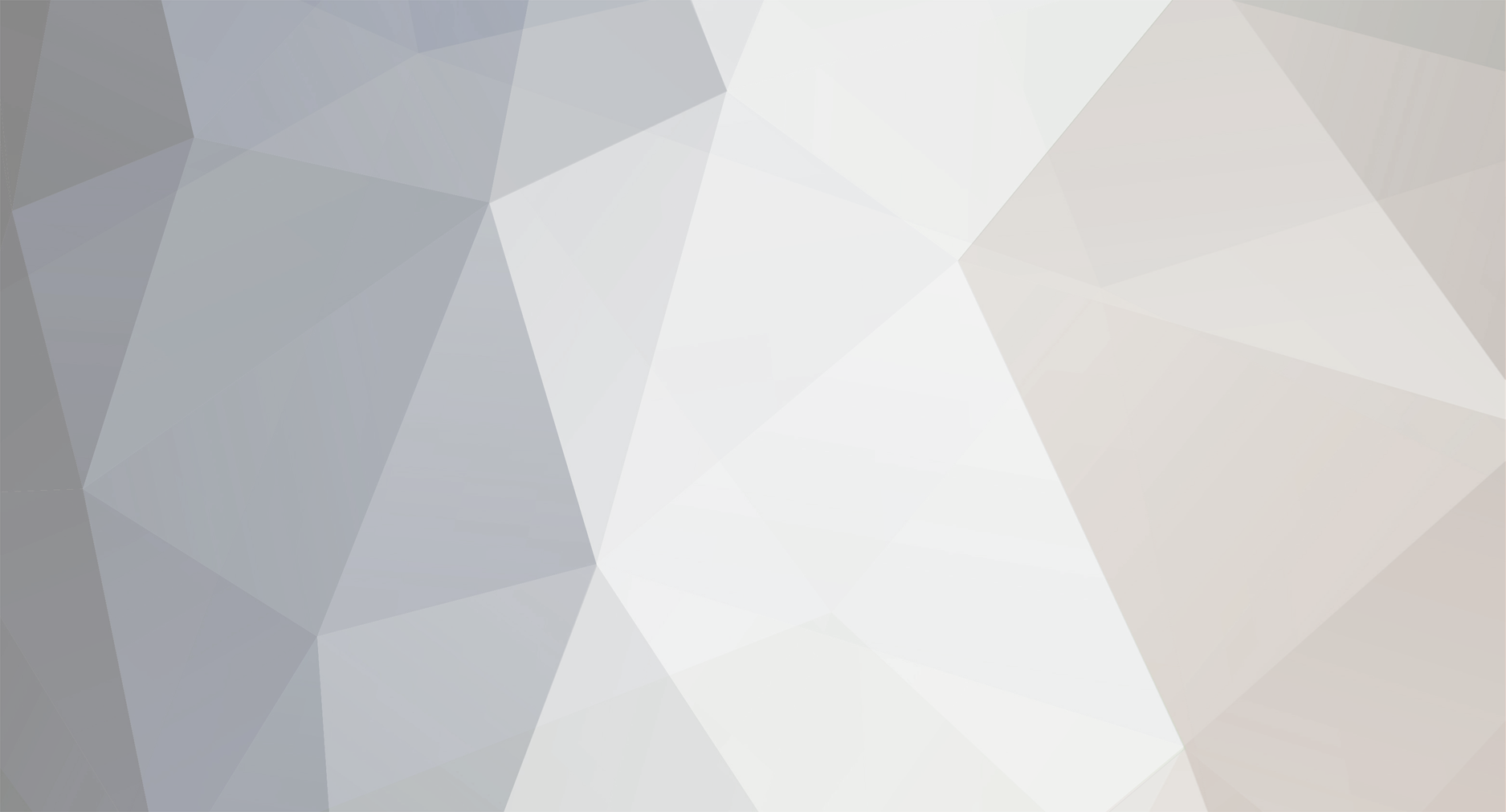
David Holman
Members-
Posts
4,217 -
Joined
-
Last visited
-
Days Won
115
Content Type
Profiles
Forums
Resource Library
Events
Gallery
Blogs
Store
Community Map
Everything posted by David Holman
-
A pox on spell checkers and predictive text!
-
My "personal jury" is still out on sound, especially at exhibitions. Probably works better for diesel than steam, because the smoke effects are still pretty crude. However, there are some things that I think could improve the sensory experience, but do not see available separately. One is either whistle or horn - a fixed unit under the baseboard with a push button to sound the standard warnings for train movements. Sound chips for locos are bespoke and hence expensive; there used to be whistle and horn units available a few years ago, but not now, it seems. Another aspect is smell. Oil, smoke and whatever freight might be carried or being emitted from local agriculture or industry. Now whether anyone really wants the whiff of the local fish dock, glue factory, sewage works, etc as part of creating atmosphere on a layout is debatable, but the gang of the sea or new mine grass might be nice.
-
Smart. Very smart indeed. Know next to nothing about the prototype, but the model looks splendid!
-
RTR or Kit, early 4 wheel CIE rolling stock
David Holman replied to Dave Dawes's topic in Irish Models
Stick with Provincial and JM Designs - they are authentic, not hybrids and you are supporting important suppliers to our modelling world. -
The JML magnifying glasses work well and are cheap at ten quid. You can wear them over your own glasses (Repair Shop style). They come with rechargeable LED lights too. Also have one of those headband magnifiers, though not as comfortable. A key thing for me is lighting, preferably the same as I will display under, so I have an LED strip over the workbench and layout, with LED spotlights on the ceiling too.
-
All looks pretty darned good to me. Louvres are nasty, awkward things to do, but the model goes from strength to strength.
-
Have taken a break from the rigging to try another task I wasn't exactly looking forward to - the water. The options included: base colour covered with multiple layers of varnish commercial resin water kit papier mache, as per KCME's suggestion earlier acrylic sheet, as suggest by ace ship modeller Gordon Gravett, indeed just ace modeller In the end, decided to go for the last one, mainly because the Acla is very heavy and its mast & derrick rather fragile, meaning a need to be able to remove it from the layout for transport. So, a trip to my local Wickes DIY store resulted in the purchase of a sheet of 1.8mm clear acrylic glazing. This then needed a suitably shaped piece to fit the space where Acla sits, along with a cut out for the hull. The acrylic is similar in structure to plasticard, in that you can score it and then snap off the piece you want. However, the method isn't suitable for the complex shapes I required, so instead used a heavy duty slitting disc in the Dremel, along with a heavy duty face mask to avoid the fumes generated. I also decided to remove the wooden rubbing beams from the quayside wall, as it is easier to put these back later, rather try to cut out the acrylic to round them. Once this piece was cut and filed to shape, it was then a case of putting the Acla on it and then drawing round it to create a space for the hull to sit in. A fair bit more filing was required for this, though it turns out that a perfect fit isn't required - just the front edge, as the back is sandwiched between the hull and quay wall, so can't be seen. Also, a small gap isn't nearly as noticeable as a a space under the hull. Once the hull shape was cut out, I then painted the underside, first with a coat of Humbrol 31 [a sea grey/green], then 104 [navy blue], though the latter doesn't seem to make a lot of difference. The water is yet to be stuck down and I also need to get back to Gordon, to find out how he adds ripples to the surface of the acrylic, but for now, the Acla looks a lot better sitting in some 'water', instead of on a sheet of plywood.
-
Wow, what a fabulous model, George! That is a ridiculous amount of detail, but then suppose in 1:24 stuff becomes ever more noticeable - right down to the toilet pan. Not sure I'm going to be chasing all that rigging, but looks like I need to add at least some now you've shown me. Fantastic work - thank you. Slapped wrist for me in not keeping an eye on other threads too.
-
The Official Irish 'Might Have Beens' Thread
David Holman replied to minister_for_hardship's topic in General Chat
Plus of course their buses reached out long after the railway closed. By the by, another reason I can't do a project like this at the moment is there is no space in the workshop, with Belmullet occupying the lower level and Fintonagh and Northport Quay the space above. Could have a go at a loco, of course, but ahead of it on my 'to do' list is the travelling crane for NPQ, the Castlederg 2-6-2T for Fintonagh, plus (as the muse takes me) Sprite and the Pay Train and/or a GSWR 4-4-0, all of which already have somewhere to run. One day maybe.... -
The Official Irish 'Might Have Beens' Thread
David Holman replied to minister_for_hardship's topic in General Chat
Mentioned the other day that the Swilly is an itch I repeatedly have to scratch and following the Cultra show found myself musing on a might have been that I've already made use of. The place is Rathmelton. A few miles north of Letterkenny, if you Google it, you find not only an interesting industrial waterfront, but also some splendid Victorian/Georgian [?] terraces that would make a rather fine setting for a model railway. The warehouse on Northport Quay is based on one of those in Rathmelton. Quite why the Swilly, or indeed the Donegal never made it there, I have no idea, but I could envisage that a joint line might have been possible, with the Swilly being responsible for traffic to Derry and the Donegal to, well Donegal. Personally, I wouldn't have the space for the long trains that both companies ran, let alone 4-8-0s or 4-8-4Ts - and the big Donegal 2-6-4Ts weren't much smaller. However, shorter trains were run, so the Swilly 4-6-0Ts and 4-6-2Ts with two or three six wheel or bogie carriages or a few vans and a bogie brake would make for a nice set up. Not much in the way of variety though, which is why a joint line is appealing because a couple of Donegal railcars [either coupled together, or towing trailers and vans], along with mixed or freight traffic would be very appealing. I can envisage a stretched version of Fintonagh [on a Northport Quay sized footprint], with a quayside as the front edge of the baseboards and the warehouses/houses behind, or a larger, Belmullet sized project allowing for longer trains and more scenery. Drawing a couple of track plans has helped scratch the itch for now and realistically such a project aint going to happen anytime soon with Northport Quay needing to be ready for its show debut in less than a year. Also, a project like Rathmelton would probably take at least two or three years, given the amount of stock required - all of which would need to be scratch built - so the plans have gone into the folder for now. However, if someone were to bring out a couple or three 7mm scale kits, then who knows?! -
N Scale Ballywillan, Co Longford.
David Holman replied to Kevin Sweeney's topic in Irish Model Layouts
Wowsers! -
Frigging in the rigging No, not the name of one of the local beers produced in the Chatham Dockyard Brewery, though I could do with a bottle or three after trying to set up rigging on the Acla. Indeed, compared to a three hour crossing in a Force 9 between Cairnryan and Belfast a week last Friday, it would be a hard choice on which I'd do again in a hurry... ... and this is just a simplified version! The Langley instructions use the term "plumber's nightmare" to describe what doing the whole lot can be and looking at scale plans, am afraid I've taken the easy way out. Goodness knows what it must be like to include it all, let alone in 4mm scale! I've used elasticated thread, so that I can unplug the main mast for transport. There should be six lines [three each side, but I've only done two] from the mast, plus one to the bow and then the cabling to the derrick. Most of these lines use a type of adjustable "turnbuckle" affair to secure them to the hull. The model boat shop in the Historic Dockyard does sell working versions of these - and very nice they are too - but at £3.50 each, that wasn't going to happen. Instead, I fabricated [bodged] alternatives by flattening the end of some 1mm brass wire and then drilled holes in each end to take loops of .5mm brass wire to which I could then attach the thread. Those a 1cm squares below. To say that all of this was a bit of a faff is an understatement - likewise drilling out tiny white metal castings of pulley blocks, while threading elasticated thread through all of this was challenging to say the least. Ultimately though, it all came together [ish], as can be seen from the two main pictures. I would hate to have to rig a sailing ship!
-
Yep, everything is a compromise - even P4, so you just have to go with what you feel most comfortable with. Ultimately, pics like the one above show there are many other aspects which, if got right, really make model railway sing.
-
Templot do track plans for 20.2mm, which they call "Irish EM". Flangways are the usual 1mm, for 00 finescale. On Fintonagh, I've used these standards without problems.
-
Brookhall Mill - A GNR(I) Micro Layout
David Holman replied to Patrick Davey's topic in Irish Model Layouts
Some really good photos here. Somebody is having fun methinks! -
I think they are merely snow spreaders - designed to clear a path either side of the track, presumably to reduce the chances of it building up on the rails again.
-
While overall, the 'Irish Market' may be small compared to GB, there is no doubt that any and every announcement of something then creates a lot of interest and enthusiasm, as per the posts above. The problem is that it may not be enough in terms of overall sales to make it worthwhile. And yet... ... increasingly we see what can only be described as 'niche' models being released over here that you have to wonder who is going to buy them? The 10800 prototype diesel, the Leader, even Big Bertha, the Lickey Banker. How many can justify one of those?? So perhaps there is yet hope for more Irish stuff, though will not hold my breath for anything in 7mm scale!
-
It is a curious fact that models of dmus and railcars are almost always more attractive than the prototype!
-
Have used the Archer rivets, which a very good, so fingers crossed for you.
-
Check out my Midland Great Western Mail Train thread (now on page 2), for how I did the lining on the Achill Bogie.
-
Adapting Hatton's coaches is almost a throwback to modelling a generation or more ago. Hornby clerestories were a case in point for any pre grouping stock and no doubt there were many who learned useful skills in adapting them, so perhaps history will repeat itself? No bad thing, in my opinion. Current models are stunning compared to what came before, but there is nothing quite like making something your own to get real satisfaction. It may just be 're lettering or numbering, a bit of detail here or there, but suddenly it is yours, not just something out of a box. Will we get the basis of some steam outline locos to go with the six wheelers? It would be nice to think so!
- 703 replies
-
- 10
-
-
-
Great pics! The combination of models and the real thing is just perfect.
-
Seemed like many of the great and good were there... and me too