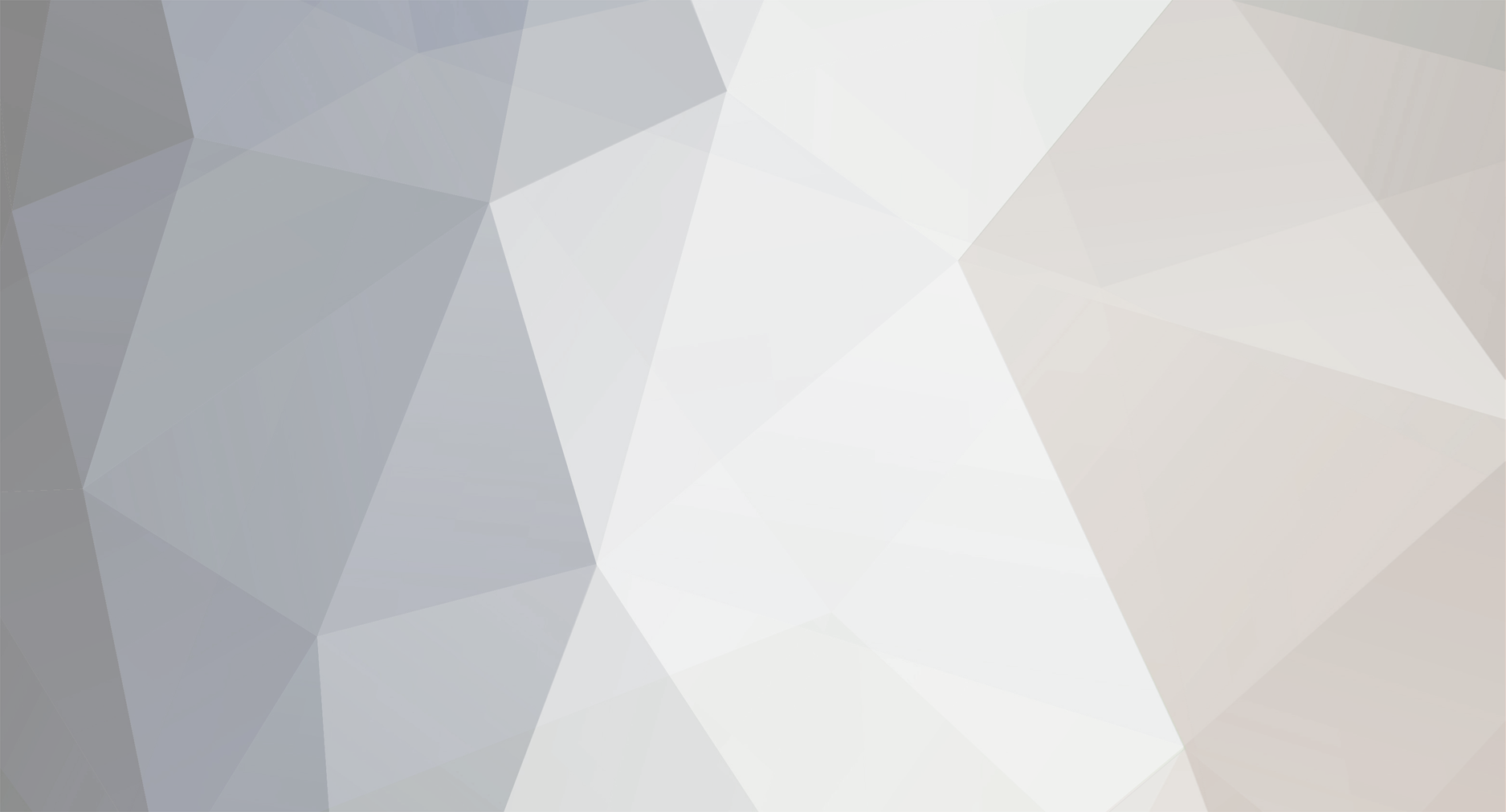
David Holman
Members-
Posts
4,218 -
Joined
-
Last visited
-
Days Won
115
Content Type
Profiles
Forums
Resource Library
Events
Gallery
Blogs
Store
Community Map
Everything posted by David Holman
-
Inchicore shrunk and moved a few thousand miles. Lovely stuff.
-
Doesn't just do great buildings then! Not surprised.
-
Saxby and Farmer supplied equipment to several Irish railways, so Wizard Models may well be able to help too.
-
Great piece of work, Ken
-
Have always used photocopier paper, cut into strips, then snipped for separate slates, works well. Slates are very thin, so paper is enough even in 7mm scale. A couple of coats of slate/tarmac enamel paint gives a good covering, with a few individual ones picked out in lighter/darker shades for variety.
-
A fine weekend at Epsom and very nice to meet with a fellow modeller of this parish, along with many others who I have got to know over the years. Epsom is a quality show, not just for layouts, but traders too. Any show that includes Roxey, Branchlines, C&L, Greenscene, Railbooks and Eileen's is worth a visit for them alone in my book. Fintonagh didn't initially cover itself in glory on Saturday. The AW tractor was running badly, while we had trouble with couplings and magnets. However, once the tractor's problem was identified to one of its pickups, it ran a whole lot better and put in a good shift over the weekend. Uncoupling magnets were gradually overcome, while a couple of wagons were withdrawn and operation rationalised to make the sequences more reliable. Hence Sunday was more relaxed and apart from the turntable needing a bit of attention, there isn't too much of a list to sort out before Reading in two weeks time.
-
Difficult stuff to find these days, but the alternative corrugated cement, I think, should still be around. Martyn Welch's weathering book suggests treating asbestos like cement. Hence mix Humbrol 110 with 95 concrete and apply with a little stippled in talc for extra texture. When dry, stain by mixing a watery tarmac or slate, or just dirty thinners and let this run down the channeling. After dry brush darker and lighter shades of the grey/brown mix across the ridges. Try weathering powders for yellow/orange lichen, but as ever, keep it subtle. A final dusting of talc always helps to tone things down. The Art of Weathering is the bible for all things colour related! ISBN 1 874103119
-
Fintonagh making its second appearance and the first of several this year, with Reading ALSRMS on 11th May, Littlehampton 18th May and 7mmNGS Convention at Burton on 8th June. Come and say hello if you are at any of these.
-
As JB says, it is the randomness that it is all about. That and being bold, but not too bold, with some fairly bright colours to capture the lichen. One thing to remember is to paint under the same lighting as you are going to display the model. Flourescent v spotlights v LEDs all have noticeably different effects. Super work.
-
That makes fretting out coach panelling look an absolute breeze! Necessary I suspect, in order for robustness. It also looks rather fab already, so all power to your soldering.
-
Looks good to me.
-
Love the black and white pictures too. Have often pondered the idea of doing a layout this way - for one thing the name would easy, it would have to be Monachrome. Even sounds Irish. On one level, it is merely a different case of 50 shades of grey (!); however, the biggest problem is foliage, as I've yet to find any source of static grass fibres or scenic foam. One day maybe and until then maybe we should follow Eamonn's lead and try photographing our own layouts in black and white?
-
They look fun!
-
You asked about doing guttering in another thread, Tony. An effective compromise I have used for years is not to bother with hollow section guttering. It can barely be seen in 7mm scale, so must be pretty much invisible in 4mm. Instead, use a strip of plastic of the right thickness and simply sand/file the front, visible edge to the profile you want. Make the strip wide enough so you can glue it to the wall, just below the roof, so it sticks out just below the tiles, slates etc. Where the ends of this guttering are visible, profile both sides of the strip, though you only need to do a couple of cm against the wall side. The rest can't be seen. Simple and effective, because the square, rear edge of the strip is easily glued to the wall and the underside will not be seen from any normal viewing angle. All Arigna Town buildings and those on Fintonagh have been done this way.
-
You could be right. However, I took the photos under two incandescent spotlights and they change the colour tone. In daylight and with 'cool white LEDs' the tone is much darker. However a coat of tinted varnish my yet be appropriate. Thanks.
-
I thought I was going to be able to post that my WLWR 6w parcels van was finished, but having just processed a couple of pictures, I'm now not sure. Rover 'Damask Red' has up until now been my go to for LMS Crimson Lake [supposedly correct for WLWR coaches], but it is looking a bit too red in the pictures and certainly not as dark as the two goods vans I now own from Castle Rackrent. All comments welcome. The model has otherwise turned out alright, though state of the art it is not. Indeed, I could not in any way vouch for much in the way of accuracy, as all I had to go on was a black and white picture of it in CIE days, when much of the panelling had clearly been replaced. The only thing I can say for sure is that the length is correct [!] and everything else is guesswork. For example, the springs and W-irons are what I had in store, while the buffers were cobbled together as well and include white metal castings for the main housing, with some extra brass tubing for the shanks and drawing pins for the heads. The laboriously fretted out panelling above the waistline is purely assumption on my part too. Indeed, I'm starting to wonder what on earth I was doing in starting it, though I guess the truth of the matter is a combination of trying something new in the way of modelling techniques and creating a train for 0-6-0 Shannon to pull. Overall then, I guess I have been able to achieve this. The first picture shows the van, complete with HMRS 'prefix' transfers [LSWR] for letters and numbers, plus a couple of Fox waterslide transfers for the WLWR crest [actually SECR, but a decent compromise, I think]. The second shows Shannon and its train [though the carriage truck needs a suitable load still], while behind is the new 101 with a GSW 6 wheeler and two horseboxes - still awaiting a WLW six wheel coach, though at least the fretwork is done for that, thank goodness!
-
Not surprised! A working diorama sounds good to me. Can see a lot of invites across the exhibition circuit - accurate, historical scenes like this are always popular and generate a lot of conversation, nostalgia etc. Thanks for the info too.
-
It really is an impressive model. What are the overall dimensions?
-
What ever you prefer, to be honest, Tony. Or even, what you have in stock. Either will work well, but do suggest you practice on a piece of scrap first.
-
I think there are basically two ways of painting buildings - mortar colour first and then pick out each stone, or put a general stone colour on first and add the mortar as a dilute wash. The latter is the technique used by scenic master Martyn Welch (The Art of Weathering). The stones can be done in a semi 'dry brush' method, when you skim the top surface with a broad, flat brush, sponge, cloth or what ever. Much depends on whether the stone is a uniform colour or a variety of shades. Once dry, probably 48 hours with enamels, the mortar colour used should be a very dilute mix. The trick is to hold the model at about 45 degrees and, using a largeish, flat brush, well loaded with paint, touch the brush at the top of the model - the paint will then run down all the mortar lines by capillary action. Repeat as required, down and across the building. Any paint on the stones themselves can easily be wiped away. Having tried it myself, it became the usual method for Arigna Town's stonework, though as always, best to test on a scrap piece first.
-
That looks like an awful lot of knitting! I think every layout builder must have jobs that just need doing and get completed with a certain amount of suffering. Ballasting and wiring certainly two of mine. Got to be worth the effort though and will add yet another dimension to a superb layout.
-
A scratchbuild, six wheel van in brass. That is class!
-
Thanks Patrick and everyone. It really IS an awful lot of measuring and cutting, though the skill level required isn't that great. Plenty of patience though!
-
Waterford, Limerick & Western 6w brake Have chosen this vehicle to complete my 'Mail Goods', a train I've poached from Castle Rackrent. With nearly 20x 7mm scale coaches under my belt, this little six wheeler ought to be straightforward. However, it is the first time I've tried rounded panelling and compared to the squared variety, it ain't easy. The bible for such things is David Jenkinson's 'Coach Building Made Easy' and with over 150 on his portfolio, he knew what he was doing. Square panelling just needs lots of microstrip and a little patience in the application thereof. Rounded panelling calls for a shedload of measuring and careful fretwork. Indeed, the first job is to draw out all the panelling on a sheet of 10 thou plasticard. The two sides are arranged base to base and once all is in place, you then cut out the panels to produce a [very] delicate latticework. To get the rounded corners, you cut each one at 45 degrees and then use a rat tailed needle file. Each panel therefore required eight pin pricks to mark the corners, so no wonder it took around 4-5 hours to get this far. This latticework is then stuck to a sheet of 20 thou sheet and left to harden overnight. The next stage is to cut out the window apertures and drop lights, with a further layer of 10 thou behind the latter, so they are inset as per prototype. Fortunately, this represents most of the hard work, for one then makes up a basic inner box structure [40 thou sides and ends, 80 thou base], with just simple cut outs for windows and droplights. The previously made panelled side are then stuck to this & after the end pieces are added. To get the right tumble home on the sides, microstrip is added at waist and roof level. So, this is where I've got to. I've also completed panelling for a WLW six wheel brake third, which is included in the photos.
-
It all seems to be coming together splendidly. Trains in an urban setting have rarely been done as well as this.