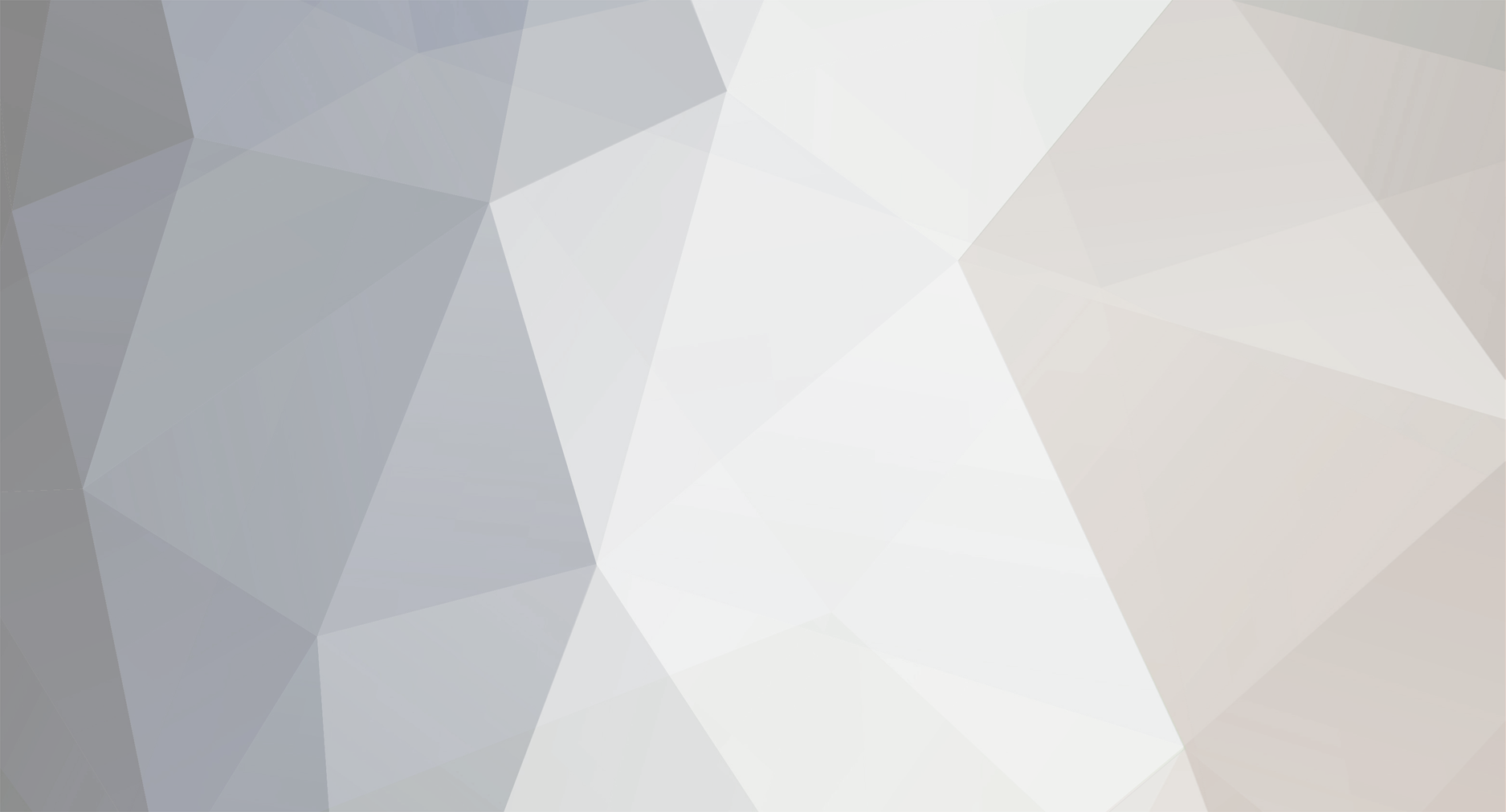
David Holman
Members-
Posts
4,217 -
Joined
-
Last visited
-
Days Won
115
Content Type
Profiles
Forums
Resource Library
Events
Gallery
Blogs
Store
Community Map
Everything posted by David Holman
-
Spent a very pleasant morning there today [once I'd dried out from getting soaked just walking from the car park that it is], with the usual mix of very high standard layouts. All manner of scales, gauges, prototypes and periods, with a great selection of traders too. Stand out for me was a new, 16mm scale working diorama from Giles Favell, of radio control road vehicles fame. Giles has not been on the scene since Covid, so it was great to see him back. A large, but simple display involved an electric powered, live steam, quarry Hunslet, with a couple of side tipping chalk wagons. These were unloaded, via a basic [but prototypical] ramp [far left on the photo], while the loco's driver was able to look around as it progressed across the scene. Giles had another animated figure which could wave its arm too. All rather splendid and very engaging. A large 2mm scale layout also caught my eye. Called St Ruth, it featured some very clever compressed & half/low relief back scenes.
-
- 10
-
-
No water, no power and certainly no 'en suite'. Different world...
-
Yes, thanks Leslie. No idea who replaced me, but if it was the logging layout, then sounds a fine alternative.
-
Apologies Kelvin! Had to visit my 93 year old mother and could not get back in time. It was going to be my 125th show, but the first time in all the years of exhibiting that I've had to pull out. Was able to give the organisers a week's notice, but guess I should have posted something here. Northport Quay's next outing will be at the To!worth Show train in early November.
-
Not an article, but was surprised, delighted, indeed - honoured - to find that in the free 2025 calender with this month's Railway Modeller, Fintonagh is the picture for July. Lovely photo taken by CM editor Andrew Burnham.
-
Won that bet with myself then! This forum just keeps on giving.
-
Apologies if this has featured before, but was going through 'Railway Bylines Summer Special No3' the other day and found an interesting snippet in an article on the ex GER Y14 /LNER J15 0-6-0s. Strong, simple workhorses, not unlike their Irish counterparts and one of them - 65464 - actually carried the CIE Flying Snail emblem. It featured in a film called Happy Ever After, starring David Niven and Yvonne de Carlo, with scenes being shot on the Buntingford branch. Sadly no pictures available in the article, but am betting someone on the forum will find some! The album also contains a fine article by Des Coakham - 'Broad Gauge Branch Lines on CIE', including some very nice pictures with extended captions. Lovely stuff!
-
As a sojourn from recent activities, the workbench has become cluttered with large buildings for the Chatham Club layout. Called 'North Circular', it depicts a North London avoiding line, following the approximate route of the road of the same name. A double track, 0 Gauge oval, there are no points [apart from the storage sidings], but a lot of scenic features, designed to act as a backdrop to passing trains around its 10m x 4m footprint. The layout is due to appear at next year's Chatham Show in July, so I've taken it upon myself to create a section with a selection of warehouses and factories, plus a small canal basin. Inspiration comes from the Metcalfe card kitts, loosely scaled up to 7mm. The whole layout is very much built 'to a standard', making use of brick and tile paper, plus commercial window frames. I use 5mm foam board for the basic structure, varying the height of each storey from 8 to 10 feet. The overall shape of sides and ends are drawn and cut out out, then the pieces temporarily joined with masking tape, to check how each one fits on the layout. Once satisfied with this, the pieces come apart for window and door openings to be cut, followed by reassembly using triangles of thick card to brace the internal corners. Brick paper [downloaded from the web and printed at home] is then stuck to the foam board with pva. I cover over the window openings and then cut in afterwards, folding the paper inside. Things like brick lintels and stone window ledges, along with large corner stones help relieve the otherwise plainness of the model. Window frames are die cut ones from 'Purple Bob'. At around 50p each, they are less than a third the price of York Modelmaking ones and come pre-coloured too. The roof is made from mounting board, covered with slate paper [same as the bricks]. Gutters and soffit boards are a single piece of 2mm plastic sheet with one edge rounded off with a file, while drainpipes are 2.5mm square section plastic rod. Below is a larger warehouse, awaiting brick paper, windows and so on. Must admit, I haven't spent hours and hours on these models, but as said earlier, they are built to the same standards we've used on the rest of the layout, so hopefully everything should blend in well together. Also shows, to new/inexperienced members that with a little effort, it is easy to produce you own models. Cheaper too. Am tempted to suggest we add a third conductor rail, as it ought to be possible to use it to enable my broad gauge stock to stretch it legs. One day maybe!
-
Couplings While it would have been nice to have authentic looking 'Zamzoodle' chopper couplings, for one thing they are quite expensive and for another seem to have been unavailable for quite a while. However, when you look at photos and drawings of choppers,, in essence they are very similar to slimline tension locks, which are readily available and much cheaper. Indeed, with friends at the Chatham Club often converting stock to Kadees, there is a plentiful free supply. The main differences are the shape of the hook and the large buffing plate - in lieu of ordinary buffers. The latter is fairly easy to resolve: a circle or rounded square of brass/plasticard suffices and the size seems to vary. Hooks seem to vary too, but all have a forward/upper extension, presumably to help the crew lift it when uncoupling. This works in my favour, because to make tension locks work with an electromagnet, I am fixing a piece of iron wire [paperclip] to the dropper on the tension lock, which extends back under the wagon. When the magnet is activated, it pulls this wire downwards, lifting the hook & hence uncoupling takes place. However, when the magnet is deactivated, this wire tends to leave the hook in the upper position, but by adding a piece of brass strip to the end of the hook [shaped to look like the prototype], balance is restored and the hook drops down again. The other thing that is needed, is a U shaped piece of wire to go over the iron wire, to keep it parallel to the rails stop it going too far and fouling the track. Nickel silver or brass is best, for obvious reasons. So far, have fitted a hooked tension lock to Railcar No10, with just loops on the trailer. It is intended these two will only work as a pair, so when the railcar is turned, there will always be a hook and loop together. Interestingly, photos often show this on the prototypes. In my case, the use of a turntable for locos and a turntable fiddle yard rather complicates matters, but have worked out that by using an 'exchange' wagon, with hooks at both ends, it is possible to remarshall a mixed or goods train without two hooks getting in each others' way. Early days, with some refining still required [mostly around the shape of the hook], but the railcar-trailer works fine, so hopefully no reason for the other stock to work as well.
-
Shades of Whisky Galore... When it came to dismantling the Red Wharf Bay branch on Anglesey, the contractors first had to replace the oak keys on the bull head track because the locals had pinched them for firewood.
-
Agreed. Doesn't matter if it is one parent or two, same sex, extended family or whatever, as long as they look after their kids, they turn out alright. Unfortunately, when the parents are dysfunctional, this rule not only falls down, but becomes self perpetuating and breaking the cycle is so difficult without the right resources.
-
With the rods on and (at rest) one side in the top position, probably very difficult to see where the pins are. I certainly won't tell. Promise!
-
My immediate thought is the usual one of perhaps the perpetrators might be chased by a couple of police dogs and the latter would be allowed to bite them somewhere painful. Numerous times. However, Mayner and LNERW1 are right - such things (wars included) ultimately have to solved by looking at and understanding the problems that created them in the first place. My teaching career was spent working in somewhat challenging communities and when you tried to understand why children behaved the way they did, there were always reasons. Trying to sort them was another matter of course. Broken homes, poverty, addiction, abuse - you name, we saw it, but trying to get support in place was another matter. There just wasn't the time, money or personnel to cope with it all. Sadly, little seems to have changed over the years, although thankfully there are still many good people out there doing their bit, so all power to their collective elbows. And thank goodness for things like model railways, this forum and the Repair Shop (to name but three), as antidotes to the ills of the world - though Peaky Blinders, Game of Thrones and Dad Army work for me too...
-
The thing about such push along train sets is their creativity. Being endlessly adaptable, new layouts are made every time and help stimulate imagination. Seems I'm not the only one to look longingly at them now! My parents moved me straight into Triang, though the Series 3 track was hideous. Did have some 000 (Ngauge?) push along stuff and LOTS of Lego. Not the stuff you see today, it was all just bricks at first, though the introduction of wheels enabled strange, not quite prototypical models to be created. Great fun though and the next day, they got dismantled to build something else. Am sure that is why I made my own stuff today - though most of it doesn't get immediately dismantled now!
-
N Scale Ballywillan, Co Longford.
David Holman replied to Kevin Sweeney's topic in Irish Model Layouts
Have done various demonstration stands at shows and remember being asked once if I'd do commissions. Being a primary school headteacher at the time, there was little space in life for my own models, let alone somebody else's. I pointed to a recently built model of Saffron Walden loco shed on my stand, advising the gent that [though the cost of materials was minimal], it probably involved about 80-100 hours of my time. I could see him quickly do the sums before thanking me and walking away. Your skills merit a decent hourly rate, Kevin. The issue is finding people willing to pay and there are folk out there with more money than time - but don't give up the music either. Jules Holland, Pete Waterman and Rod Stewart seem to combine music and model railways fairly well... -
As an alternative to battling the Barclay, decided it was time to address the new uncoupling system. Kaydees and rare earth magnets have worked quite well, but Swilly and Donegal stock couplings sit higher and Kaydee No 5s are no good. Their S scale version would probably work, but needing to be imported, the cost looked prohibitive. Hence am trying tension locks and will adapt them both to work with Dingham electro magnets and look more like narrow gauge 'chopper' couplings - more of the latter later. First job, having bought the magnets from the Gauge 0 Guild stores and some push to make switches from my local model shop, was to decide where everything would go & how to put it all together. Considered trying to fit the switches into the existing mimic panel, but space is already tight, so cut out space for a second panel next to it. Then had to decide where to site the magnets, which are pretty much where the permanent ones were. Wiring it all up was, for once, fairly painless - just needed to add a 15v socket for the magnet power and a separate set of wires, plus a pair of 9 pin computer plugs. However, a small part of the process involved reversing a Tortoise point motor to make room for the magnet just outside the train shed. Simple enough? You'd think so, but it became a real case of the south end of a north facing horse. Turning the motor through 180 degrees sounds straightforward, but it reverses the terminals and combined with it being half a crossover and both motors operated from the same switch, it really was an accident waiting to happen. Three days of trial an error later, I finally discovered this evening that the issue was not the motor terminals, but the double pole-double throw switch on the panel that needed reversing... One of these days I'm going to convert to battery power! Photos show the undersides of the boards, with a ridiculous number of wires beneath. I put tag strips between switches, plugs and fittings, keeping a careful records of where each wire connects to/from. Hence it doesn't matter what colour wires are used - you just look up where they start and finish. The clothes peg holds a cable connector The others pictures show the new panel and some of the magnets. Needless to say, the latter still need to be cut down to sleeper height.
-
Lovely diorama - only goes to show there is always room for a model railway. Thought you were going garden railway at first, but using the great outdoors for the photos works a treat.
-
Swords, Phibsborough and Adelaide
David Holman replied to Sheldrake9er's topic in Irish Model Layouts
Lovely stuff! -
Swords, Phibsborough and Adelaide
David Holman replied to Sheldrake9er's topic in Irish Model Layouts
Nice to know that Ga!teemore and I aren't Roger's only customers! The signalled is rather splendid, so we certainly need to know more. -
Few of us have enough space for our projects, so compromise and flexibility is usually the key = good ideas! Your modules will be a nice way of experimenting with scenics, regardless of whether they get much use. Getting a first exhibition invite can be tricky, though mostly it is about finding who runs them locally. Easier this side of the water, where there can be anything up to 30 or more show every weekend throughout the year. Just look at the Events section at the back of any Railway Modeller. We probably have more shows in a month than the whole of Ireland has in a year and another factor in this is as soon as you attend one show,, several invites occur for future ones. So, talk to the organiser/club running your nearest local show and tell them what you have. They will want to see photos, but also need basic information like layout size, power requirement, lighting, is it self supporting, number of operators and likely expenses. On the latter, always better if it can fit in your car as van hire is expensive. If a show is a long way from home, overnight accommodation is a factor too, for you and/or the organiser. Once you have invites, plan carefully. I've done well over 100 shows and still don't always get it right. Taking a layout apart, bouncing for miles in the back of the car to a show, reassembling and hoping it will then work is not a gimmie. Practice (ie play trains) at home, so you know there is a good chance it will be reliable, but be prepared for things to go wrong. At the very least a spare controller and spare engines. Organising setting up to minimise time and effort is both a science and an art form! And above all remember that when taking your layout to a show, you are on display to paying customers, who will want their money's worth. I could go on, but honestly, it is great to see you wanting to get into exhibiting and it can be very rewarding and well worth the effort because you learn something new every time.
-
Ace modeller Gordon Gravett learned CAD during his creation of the epic Reseau Breton layout, Pempoul, reasoning that to cut down on the amount of scratchbuilding required, commissioning his own bespoke kits would be a time saver. Everything from locos and wagons through to stuff like fencing and other scenic items got drawn out and sent off to the etchers. Never asked him about the costs, but know he has found it worthwhile, because he continues to work this way. Those who produce multiple kits for sale, obviously want some remuneration for their efforts - an quite right too, because the creation of the CAD file takes a lot of time. The fact that a CAD file (or even something hand drawn) can be resized is a tempting idea for the few of us who would welcome the option of reducing the amount of metal fabrication required for a model. Shame therefore that there is no 'middle path' where files could be purchased by individuals to commission their own etches - though issues about copyright or even the unscrupulous pirating drawings to producing their own ranges are obvious.
-
Thanks folks - as you can see, it has been a challenge, making a lot of it up as I go along, especially that chassis! The lack of components to create a 7mm scale, 21mm gauge, outside framed chassis proved the major stumbling block - that and a similar lack of info on outside framed chassis generally in my preferred scale. And I did look, honest! Continue to find it remarkable what is out there though, like the Worsley etches for the body while special mention to Roger Cromblehome for sending me his CAD drawing of the chassis, without which am not sure I'd have even considered the project. Hopefully, I now know enough to tackle the Kerr Stuart 4-6-2T, which is the only other Swilly loco that will fit on my turntable. Got an outline drawing and a good selection of photos, but if anyone knows of anything suitable, by all means let me know!
-
Murphy model 141 poor running question
David Holman replied to trainboy's question in Questions & Answers
Agree with the above, though meths soaked on a cotton bud, then pressed on each wheel tread (and rear) while they are turning, also does the trick. A couple of crocodile leads from the track is all you need of you don't have a wheel cleaner set. -
At long last, the Barclay tank is about where I want it to be. The chassis continued to put up a fight, but with a day at home while we had a plumber in to move a couple of radiators, an opportunity to do lots of fettling meant I got things there or thereabouts. The bogie has needed a piece of brass strip to provide a bit of downward pressure on the front end & it ran even better where I removed a large piece of crud from one of the flanges. Dummy springs and brake gear largely completed the job - though couplings still need adding. After all the work on the chassis, paintwork on the body needed serious attention, so after a clean up and a respray in matt black, I sent off for some lining and lettering from Fox Transfers. These duly arrived the very next day and while the lettering [Londonderry and Burtonport Extension Railway No2] was simple enough, the lining was a real trial of patience. Swilly loco lining seems to vary on every loco over the years, so while I'm not going to claim any fidelity for No2 during my chosen period of the later 1940s, I'm not going to lose any sleep over it either. Then thought long and hard about the weathering, because Swilly locos were generally well kept, but looking at colour photos, it is clear that paintwork wasn't always in ex works condition either, so it was back to Martyn Welch's excellent book The Art of Weathering for ideas. The under frames were the standard mix of Humbrol Gunmetal, leather and black - plus a dusting of weathering powders. Areas like outside cranks and cylinders were picked out in Metalcote gunmetal [2004]. Being too lazy to set up the airbrush for what was going to be little more than a couple of light passes, I instead used the stippling technique. Metalcote gunmetal, gloss tan and roof dirt [mixed 2:1:1] was lightly brush painted over the whole body, apart from the smokebox. The trick then is to use a 'flattie' brush to stipple the paint, all over until it dries, which then gives a nice, fairly even, covering. You have to do small sections at a time, but for me it works quite well. The finishing touch, once the paint has hardened overnight, is to polish the surface using cotton buds, fingers, cloth or whatever seems appropriate. This give a nice sheen and the loco, while work stained, still looks well cared for. The smokebox gets the same treatment, but with ordinary gunmetal. So, there we are - it's been a long haul, with a completely new chassis and probably three different paint jobs, but I'm really pleased with the way it has turned out. Indeed, while it is all still fresh, I probably ought to have a go at the Kerr Stuart 4-6-2T, but something different [and less stressful] may well be appropriate before that. I've rather indulged on the photos, but, after all the effort, it is nice to see a model that has finally turned out ok.
-
Very much agree with the above and overall you should expect to build multiple layouts as skills improve and tastes change or develop. It's all part of being creative. Easy to say here, but scenery shouldn't be complicated. Any contours are just a case of building up layers with whatever scrap materials are to hand, then covering it with plaster/filler/papier mache. Use a small bit of board to practice beforehand, so you can try various scatter material too. Surprisingly quick and satisfying to do. Indeed, why not make a removable section of scenery, on a piece of thick card or thin board, that can be dropped in place when finished? Will need to be stuck down and blended in eventually, but will keep some of the mess away from the layout.