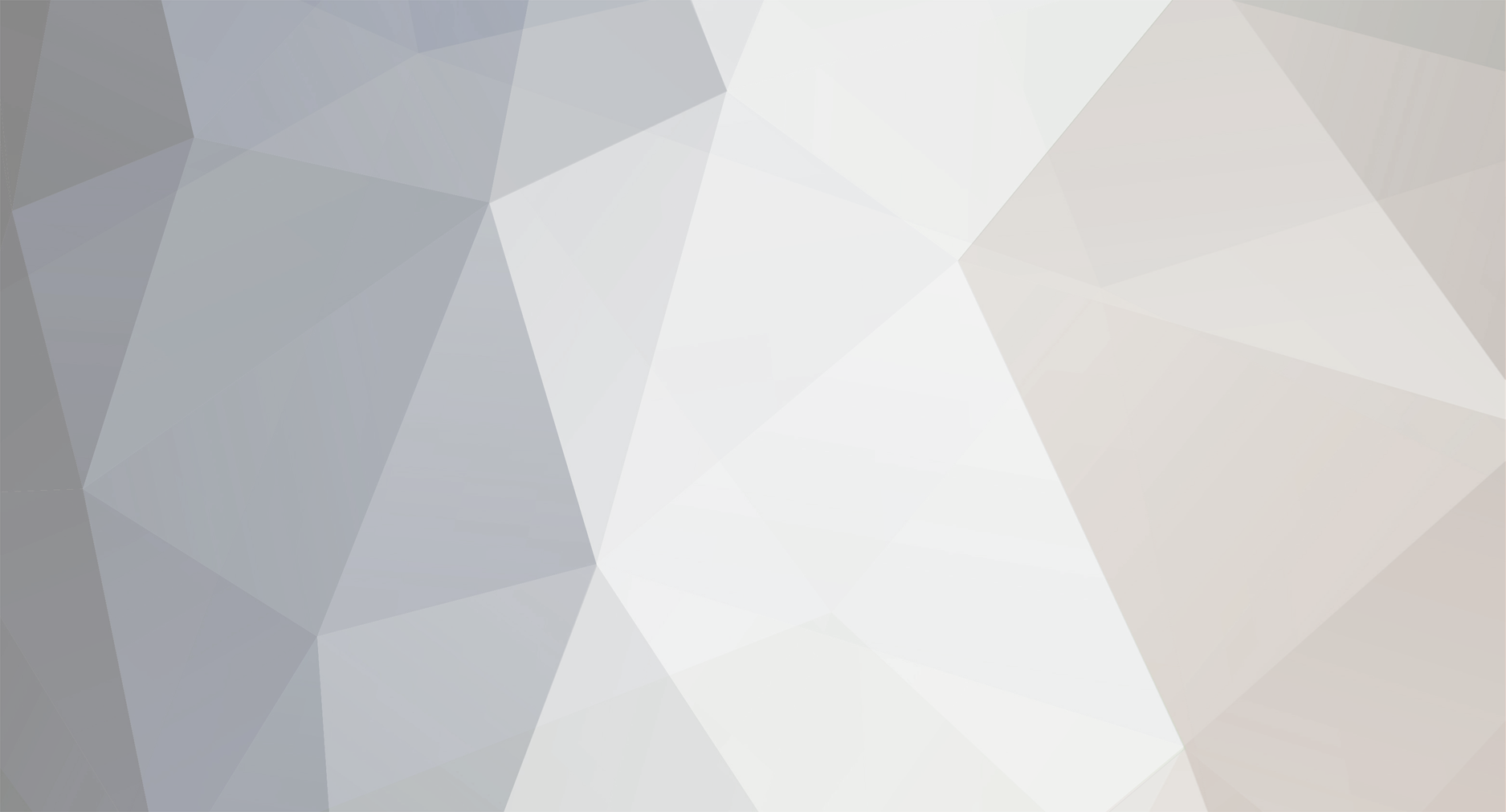
David Holman
Members-
Posts
4,218 -
Joined
-
Last visited
-
Days Won
115
Content Type
Profiles
Forums
Resource Library
Events
Gallery
Blogs
Store
Community Map
Everything posted by David Holman
-
Martyn Welch very much shows the way to go in his Weathering book. Put on the base colours first - wood/primer/rust/darker original etc - then gradually rub back to reveal once dried. Glass fibre pencil, fine wetndry, T-Cut or whatever. That simulates actual wear. It should only be dirt that goes on top and rust comes through from underneath.
-
Stoke Summit was a rare layout where people would stand and watch for half an hour and then go back for more later. I know I did. Even saw folk noting down loco numbers on more than one occasion! And yet all it was, was a double track mainline with a downside loop. No station, few buildings, but a very large fiddle yard. As a watching the trains go by layout, it has not been bettered. Roy also wrote some forthright articles about managing big layouts and the strain they placed on locos in particular. These perhaps didn't appeal to the rivet counter end of the hobby, but made absolute sense for his layouts and those like them. A significant presence in the hobby who will be sadly missed.
-
Fascinating thread. For what it's worth ' Gauge 1NG' was something I explored for a while, though never got any further than a few track plans. However, the whole Gauge 1 thing has been pretty nebulous over the years - anything from 10mm/ft on 45mm track (clearly wrong), or 1/32 (double S scale), plus the modern Aristocraft diesels (very tempting at the price!), which are approx 1:28ish, I believe. Therefore doing 10mm/ft on 0 gauge track isn't going to be far out and certainly far better than other scale/gauge combinations I could mention! If building a layout, then 6ft radius points need about 18"/45cm of space, so it is then possible to quickly work out how much space a terminus layout would need. Doable in about 3metres, plus fiddle yard maybe? As others have said, wheels will need exploring, but as many NG locos had outside frames, then the correct number of spokes should not be a problem and Slater's 7mm wheels of the appropriate diameter ought to be ok. All in all, could be the start of a fine project!
-
Getting a really worn appearance like that is just as hard as doing a pristine one and easy to over exaggerate too. This one is nicely subtle and very convincing. Fine job.
-
...but then not sure even a trader would have the kilometre or so required! Worth the effort though, as it already looks stunning.
-
The 'drumlins' book is great, but even better is 'Narrow Gauge Album 1950-1965 in Colour' by Michael Whitehouse, son of the great photographer, Patrick. Chapter One 'To Arigna for Coal' has text from JC Boyd with simply jaw dropping photos, the quality of the colour is just astonishing. With sections on the Isle of Man, North Wales narrow gauge, English ironstone plus both the Donegal and the West Clare, it is possibly the best album ever on the narrow gauge. Lightmoor Press ISBN 9781911038 49 8
-
Have both books - more accurately A4 notes and drawings in a binder - and there are indeed lots of Irish NG drawings, including several railcars too. Well worth having.
-
For my 21mm gauge Fintonagh stock, I use Branchlines wagon chassis (correct for the CVR) and 14mm wheels from the same source. However, I've replaced the steel axles with 2mm diameter brass rod because I'm using Kadee couplings with rare earth button magnets for uncouplers and don't want the magnets grabbing the axles. Have found it easy to make pin point ends to the axles by either spinning the rod in a drill chuck against a file/sandpaper, or twirling the axle between my fingers against a slitting disc in the drill.
-
Looking good! Reassured about both the tender chute ( just as confused in 7mm scale) and the fixing hole, though only found too late it lines up neatly with the rear axle...
-
A build of epic proportions! Both enjoyable and enlightening to follow, with all sorts of clever hints and tips along the way. Most of all though, a fabulous model with quality all the way through. Well done. REALLY, well done. Be very proud. So, what's next dare we ask?!
-
Cavan & Leitrim style 3ft track making
David Holman replied to PorkyP's topic in Irish Model Layouts
I made Fintonagh's 21 mm track from Peco Code 83 FB rail - they sell it as conductor rail, but it works fine for copper clad track and points with both 4mm finescale wagon wheels and Slater's three foot gauge, 7mm scale wheels. Used Templot for point drawings. They do 'Irish EM', 20.2 mm ones, but it was easy to enlarge them to 21mm on the home printer/copier. The only difficult hot was getting a suitable roller gauge, but eventually, someone turned one for me on the club lathe. What I would say is even using 4mmFS standards, clearances are tight. Wheel back to backs are around 19.5mm and anything more than 0.1 mm outside that can cause derailments, whereas in broad gauge (36.75mm) on code 100 track, I can get away with nearly 0.5mm either way. -
Excellent!
-
Great work - just goes to show that even in 2mm scale, the correct gauge has a real impact. Appreciate it is not for everyone, but does make a difference.
-
A trick of the light, Mick. Track wiring is red and black, network wiring is red, white and black, while for some reason, the servo leads are red, brown and yellow. My mobile phone case is VERY pink though, but only because that was the only colour they had. Even so, still manage to lose round the house!
-
More Wiring Trials Spent the last week faffing about with point control wiring. I've invested a fair wedge of my hard earned on a Megapoints control system. This has included: A custom made control panel, complete with Belmullet lettering and mimic diagram A master control board, switches and LEDs to go in the panel and which work all the points and signals via a single network cable. Three Servo Driver boards, each controlling four points or signals, which go under the baseboards. The Megapoints stuff also requires its own 5 amp, 12v supply, plus several network cables to join the Servo Drivers together. Hence the under baseboard wiring has grown a bit, to say the least. However, the servos only cost £1.80 each [about a tenth of the price of Tortoise point motors and associated switching], while the entire system is pretty much 'plug and play', requiring the minimum of soldering. It is expensive though. So, what I now have is as follows: A mimic control panel with a lot of spaghetti inside. This comprises leads from the push button switches and LED indicators [green/green for point routing and red/green for signals], which go to terminals on the main processor. A 12v supply goes in from the transformer, with just a three strand network cable going to the layout, instead of around 30= wires if I had used ordinary point motors and toggle switches Baseboard 'C' [nearest the fiddle yard] will have the mimic panel fixed to it with a couple of quick mount plates. A single servo driver has four leads going from it to the three arm signal as seen on Arigna Town, plus the main turnout on entry to the station. There is then another three strand network lead going to the middle scenic board 'B'. Baseboard 'B' has two servo drivers. The first one has two leads to the double slip, with the other two going to what will be two new starter signals at the platform end. The second servo driver covers the point to the loco shed on Baseboard B, then two more network leads go to Baseboard 'A' to work the loco release crossover and the point to the end loading dock off the bay. On the one hand, much of it is fairly straightforward, but with my aforementioned ability to get things back to front, there has been a fair amount of bad language and a lot of head scratching to get it all set up. The system is quite clever, because it enables you to reverse the switches to ensure the lights on the mimic panel are going the right way, while the signal controls allow you to have them bounce and do the 'double pull' as seen on the real thing. In addition, the range of movement on the servos is controllable too - handy for ensuring points close properly. The downside appears to be that the servos, while cheap, may not be all that reliable, so I have ordered some spares already! It may well be prudent to protect the servo drivers with some sort of cover too, eventually. The photos may, or may not make the above clearer...
-
Puts my drawer of tinlets to shame and have seen exhibition stands less well stocked!
-
I seem to be dribbling....
-
Gresley Beat apparently needs two seven ton lorries, so a way to go yet maybe. There's plenty of us that would love to see Barrow Street. Magazine articles at least, hopefully
-
Might need to book Pickford's too!
-
Love small projects like this. A chance to focus on fine detail and use/display all those fine models.
-
The knees of the bee, the mutt's nuts, the... Fab.
-
Chris Nevard is a scenic master in the Gordon Gravett class, with many cameo layouts and dioramas to his name. Using Das Clay looks ideal because what you want is a very fine surface, which even using N gauge cinders would be too coarse. Sifting in a bit of fine sand might be appropriate in a few places, while an electrostatic grass machine works wonders for foliage. Peco have a new Mini version out, which is good for tight corners and small areas, though the original Noch puffer bottles remain surprisingly effective. Beware bright shades of green though. However good Ireland's liquid sunshine is for the green stuff, I'd still err on the yellow/straw shade of things. And get the lady in your life to check the tones. Gentlemen beyond a certain age lose the ability to see shades of green, while our women folk would say we don't have much colour sense in the first place!
-
Organised Chaos Or wiring, in other words. Wiring for me is a necessary evil. Trains won't run without electrickery, but my knowledge is of the 'just enough and no more' variety. However, the biggest problem is my mild dyspraxia - or at least that is how I think of it. Clumsy, a bit, but the main problem is really struggling with anything 'handed'. If there are two ways to put something together, I will do it wrong first, no matter how many times I think about it, while anything with rotational symmetry is a nightmare! Assembling flatpack furniture always takes twice as long as it should do... Wiring a layout is an exquisite type of agony, because you have to reverse what is on top of the baseboard when you wire underneath and likewise plugs and sockets. So, am feeling rather pleased with myself today, because I've managed to rewire the Arigna boards and they work!! I should have taken pictures of the bird's nest of spaghetti that had grown under the original boards, but suffice to say what you can see below is a whole lot neater. Those who know about such things will no doubt have done the job differently, but it works for me. Changes from Arigna are as follows: There is now just a single controller socket on the front of the station board, instead of the four that were there previously. This profligacy was simply because firstly Arigna was operated from the rear at shows, but I needed a front socket for home use. Doubling up both was to accommodate my spare controller, which had a different plug on it. I am sure you are already wondering why I didn't fit the same plug to both controllers, but it seemed like a good idea at the time. I have long realised my mind doesn't always work logically! A Tag strip with 72 loops [2 x 18 double strips] has been fitted under each board. All wiring goes to these first & this is then split and sent to track feeds and baseboard sockets. Staples help keep the wiring fairly neat. Wiring is now just red and black - one colour for each track, with a wiring diagram that tell me which tag strip goes to which feed, socket, etc. Under the Arigna boards, colours were rather mixed at random, using whatever I had to hand at the time. I know... While only 8 wires goes from Baseboard 1 to Baseboard 2 [and only 4 wires from 2 to 3], I have used 15 and 9 pin computer plugs and sockets to keep any stray wires away from touching each other. Baseboard 2's tag strips have leads going from them to the other two boards. In storage or transit, these leads are kept tidy by using clothes pegs hot glued to the underside of the boards. Point and signal control will be by servos, using Megapoints units and a custom made panel. This will be on Baseboard 3 at the fiddle yard end. The Fiddleyard operator will also be the signalman, with the driver at the station end, where all the uncoupling magnets will be too. Although I have no intention of using DCC, it would be nice to have a steam whistle/diesel horn unit, for the driver to call attention to the signalman. Better than shouting down the layout, methinks... Chances are, the signalman will also work the turntable, as it will be easier to align the tracks than from 10 feet away, where the driver will be. Anyway, the above has taken me much of the last week and a lot longer thinking about it. And yes, I did get everything back to front on the first board and had to redo it. Needless to say, a few rude words were uttered. More than a few, in fact. The photos show the undersides of the boards and the chaos that reigned all around me while I was doing it. It took rather a long time to tidy up!
-
With the addition of a fiddle yard, plenty of shunting layouts have been operated in less. Equally, methinks you are having plenty of fun with the modelling and that is what it is all about. Coming on beautifully.
-
Some lovely detail there.