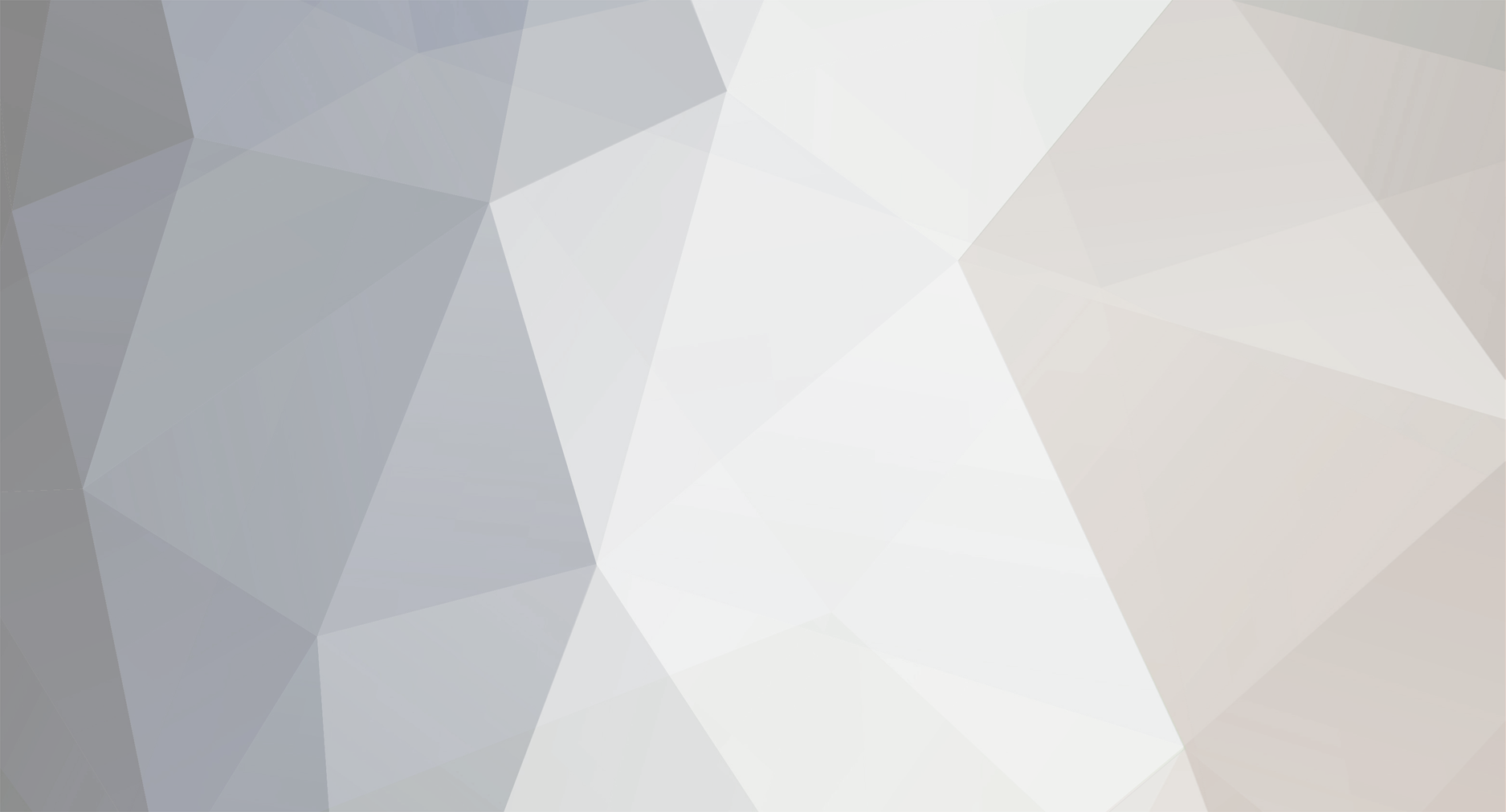
David Holman
Members-
Posts
4,218 -
Joined
-
Last visited
-
Days Won
115
Content Type
Profiles
Forums
Resource Library
Events
Gallery
Blogs
Store
Community Map
Everything posted by David Holman
-
Bit of negotiation always needed beforehand and to be fair, this only happens as a first time set up. It is just too much of a pain to lug everything out of the workshop.
-
Presentation & Transport Taking a layout to exhibitions is a curious form of madness. You spend hundreds of hours making the thing, only to separate it into parts, load it in a car or van & then bump it across the country to the venue, before [only a few hours later] doing the whole thing again to get home. The last few weeks have been working towards all this, so have included a few photos of what I do, mostly based on many years hard experience and watching what other do too. I think my ideal layout would either be an inflatable one, or maybe like a pop up book - quick to set up and take down, so you are on your way home almost as the last punter departs! The reality is that getting set up inside an hour and being on the way home in half of that is about as good as it gets. Larger layouts can easily take two or three times that, even with a big crew. Setting up Belmullet is as follows: It starts with two adjustable steel decorator's trestles on to which are placed two long [T section] beams. Being over 3.5m long, these break down into shorter sections for transport. The four baseboards are crated up in pairs, using 6mm plywood rectangles. Once separated, the middle scenic board goes on the beams first, followed by the two outer ones. Alignment is by pattern maker's dowels and M6 bolts and wing nuts hold everything together. The fiddle yard board, which has its own fold down legs, is then bolted on. After, the five 'skyboards' are bolted to the back and ends of the scenic sections Lighting comes next. There are two folding brackets covering the two scenic baseboard joints, with a plywood panel on the front at each end. The former go on with quick mount plates, the later are bolted. Three pelmets, with integral LED light strip are fitted with QM plates. then a second strip of LEDs is added above the centre line of the layout. The drapes go on next, to hide the underside of the layout, then three display boards, with info about the layout and models are added to the front. Underneath, all the electrical connections need to be plugged together and likewise the control panel and loco controller All this, along with four large shopping bags holding the stock boxes, plus what I call the 'sundries crate' [full of odds and ends, plus various transformers] and the all important tool box, has to fit in the car. In my case, this is a Skoda Karoq which, once the rear seats are removed, assumes van like proportions. However, as the last few photos show, space it tight!
- 179 replies
-
- 16
-
-
-
-
Fascinating. More please!
-
Seeing these on Patrick's layout got me wondering. When were they introduced in Ireland? Reason being that Parkside do a 7mm scale version and I happen to have one. If they appeared by 1957, I might be able to justify one on Belmullet and this could add another 'transferable' wagon kit, alongside the Slater's tank wagon. Any later than that and will have to wait until my early 1900s stock building become 1960s and that certainly ain't happening any time soon!
-
Make my guttering from sheet plasticard. Use 80thou in 7mm scale, so 40 would be ok in 4. Cut a strip wide enough to just project beyond the roof tiles when the other edge is pressed against the wall. Next, round off the outside edge to look like the guttering. Where the inside edge of the gutter can be seen, cut this to size and round off, but only for a couple of cm. The rest cannot be seen, plus the inside edge of the strip glues nicely to the wall of the building. Downpipes are made from round or square section strip, with joints made by adding thin strips of masking tape, while the fixings on the walls are just more small pieces of plastic strip. Once painted (black for the top of the guttering), such deceptions are very effective and don't take long to make. As for tools and materials, my go to is always Eileen's Emporium, who provide excellent on line service and better still at shows, where an A1 sheet of plasticard can be bought for the same price as A4 in your local shop. Slater's also have a good range of materials and their service is excellent too. For windows, York Model making are hard to beat, especially with the cost of microstrip being so high. It is almost as cheap to buy York Windows as it is to make them yourself in 7mm scale.
-
The Chatham Club's 7mm layout is a double track, two metre diameter circle, which we superelevated by using one millimetre shims and seems to work fine, even when we add the 5m straight section to make it an oval. No points mind, apart from the storage loop. Ignorance is bliss, methinks, having read Robert's excellent notes.
-
Splendid - and nice to see all the scenic section. Good job it is fairly small, otherwise would expect to read of a national shortage of scenic materials! Shows how a combination of artistic skill and careful observation really bring a scene to life.
-
Not in 7mm scale.
-
Boxes While nothing much to report of late, have nevertheless been busy trying to get Belmullet ready for its debut at Uckfield in mid October. This has mainly been about presentation, so I've been building what the theatre calls a proscenium arch, or a sort of picture frame in other words. Two side panels, a pelmet, plus three display panels to go along the bottom & all needed priming and painting, along with separate sky boards to go along the back and sides. Hopefully, I've got some LED tape arriving tomorrow, so this can be added and wired up to provide the lighting. Fingers crossed, everything will be ready to be assembled on the layout in a week or so's time. Meanwhile, have been attending to the challenge of providing boxes for all my stock. At exhibitions you can see everything from the sublime [custom made wooden boxes holding stock in neat, foam lined spaces] to the faintly ridiculous - usually a hodge lodge of shoes boxes, ice cream tubs and the like. The former very expensive, the latter often free, though far from ideal... Over the years, I've standardised on foolscap box files [for rolling stock] and 'Really Useful Box Company' four litre/A4 sized plastic crates for locomotives. Both seem to work quite well and you can get four of each into one of those large, reinforced supermarket shopping bags. 7mm scale stock takes up a lot of space & more than once I find myself envying those who model in 2mm scale, where everything would probably fit into a single box - I currently need 16... At various times, I find myself looking around DIY stores for alternatives & recently came across a very nice looking hinged, plywood box in a store called Hobbycraft. After much pondering, decided to try one & have found that, by adding a home made inner tray, I can get all my Fintonagh stock inside in two layers. Anyway, here are a few pictures that should clarify.
-
Fascinating, as ever. The T&D tank might be old, but still looks the business.
-
My 7mm scale, 21mm gauge layout Fintonagh, uses code 83 rail - as opposed to the code 100 generally used in 7mmNG. Not much, but visually, it does make a difference in portraying lightweight track. Likewise using code 100 rail on 7mm broad gauge. Indeed, originally used code 100 on a standard gauge 7mm scale light railway project and was once asked at a show if it was broad gauge! The moral of the story has to be that you use finer section rail where appropriate and those folk not able to go proper broad gauge can make 4mm scale track look much better by using Peco code 75 or equivalent, as exemplified by Ballyercal and others recently.
-
Have done a fair few articles for RM over the years and the gap between acceptance and publication can be anything up to a year. Where possible, they like to do some articles that come out just before an exhibition (remember those?), but also like to group things under various themes. Was lucky enough to be given a private tour of the Peco site by Andrew Burnham a few years ago. It has a real 'family' feel about it and the workforce is largely local, but it is also highly professional, with lots of cutting edge equipment alongside old school skills. The RM offices are surprisingly small, but then everything is computer based, with printing and so on off site. Pecorama itself is a delight. The gardens are stunning and the miniature railway is fantastic. Well worth a visit if you are in the area.
- 463 replies
-
- 6
-
-
-
- ballyercall
- layout
-
(and 1 more)
Tagged with:
-
Went there eight years ago, aiming for the 11am train and arrived slightly late to find nobody around, but the railcar in the platform. The door to the portakabin office was open and so went to ask if trains were running. The lady inside responded in a lovely soft Donegal accent 'Oh yes, I'll get the boys for you'. Two giant young chaps, who could easily have graced the all Ireland rugby front row, ambled out of the shed and took my wife and I up the line and back - we were the only passengers... The setting is fabulous, the railcar simply iconic. If the operation is to survive though, then services need to be reliable. It is a long way from anywhere and while the trip to Fintown is stunning, I sympathise with anyone making the effort only to find it shut. Running a preserved railway is challenging enough, doing so with just a single railcar and diesel tractor seems a bit 'wing and a prayer'; likewise minimal staff. Add in the remote location and however attractive that is, you have to wonder. I wish them well, but without proper funding, suspect the line will always struggle.
-
Depends on the prototype, location and period, Colin. Could be anything from lightweight, flatbottomed rail (say Code 60), through Code 75 bull head, for general purposes, to maybe Code 83, which Peco sell as conductor rail, for modern flatbottomed track. Pretty much anything but Code 100 in fact! Indeed, having just looked at the latest Ballyrecall photos, track work there is an object lesson on how Peco 75, when well ballasted and weathered, can look very effective, even when masquerading as five foot three.
-
Simple, but so effective. I don't normally like photographic backscenes as they are often too bright, but the colours seem more muted and fade into the distance, so it works a treat.
- 463 replies
-
- 4
-
-
- ballyercall
- layout
-
(and 1 more)
Tagged with:
-
Take a well versed historian, create a model railway and bring it to life with anecdotal scenes. It's like looking deeper into one of your books, JB.
-
Very fiddly and a pain to do. Not always (often, even) seen on layouts, but makes an important and subtle difference when it is. Fine work.
-
Fine effort Ken, especially when it started looking like it was covered in roofing felt!
-
Yep, keep the post coming!
-
The last couple of weeks have been busy with other stuff, including the need to get Fintonagh ready for the Bexhill Show, but attention now turns to ensuring Belmullet is ready for its debut at Uckfield on 16th & 17th October. At least, that is the plan anyway. Hence, the turntable has been bedded into the surrounding scenery, while I've done bits and pieces to disguise the baseboard joins. In addition, the leading edge of the baseboards has been given a hedgerow border, the latter made from rubberised horsehair covered in scatter material. In order to make the layout presentable, the front will be given a pelmet and side wings to frame the scene, while skyboards will raise the rear scenery by about 30cm. These will all be separate pieces that will need to break down for transport. Speaking of which, I also need to ensure the layout will fit in the car. This is a Skoda Karoq, which has removable rear seats, effectively turning it into a small van. However, with the baseboards crated up in pairs, plus trestles and supporting beams, pelmets, lighting and information boards at the front, some careful planning is needed - especially as, in having the layout with two distinct operating periods, there is quite a lot of stock to take with me too. It is at times like this, I find myself envying Angus and his 5p workbench as I'm looking at around 18-20 A4 box files.
- 179 replies
-
- 21
-
-
-
Mine arrived yesterday and very good it looks too, with plenty of inspiration for layout builders.
-
So, that's what you've been up to. On the strength of Rails to Achill, it goes straight to the top of my wish list. Amazon had three a minute ago. Now down to two...
-
More 3D printed sophistication! Ken, J-mo and now Fergalm. The traditional solution would be to cover everything in clay and then hand scribe all the stones, so love the creative thinking to design a roller - and dare I say, one that could well have a commercial application.As Fine work all round.
-
We seem to be entering a new age. Must confess that until recently, have been sceptical of 3D printing, simply in terms of the quality of models I've seen in the flesh, or in photos. Quietly though,, over the last couple of years, the fruits of CAD in laser cut kits, creating your own etches (Gordon Gravett has been doing this for a while) and now complete, printed models are really proving what can be done. Don't let anyone say it isn't proper modelling either, because for me at least, it is applying new skills to traditional ones. All power to your elbows, Ken!
-
Extraordinary, remarkable, amazing! There was me thinking you were 'just' having a bit of fun with CAD and here you are displaying a finished, painted model on some track and scenery. The Newman system says nothing about propulsion though. Is the slider being moved by hand, or could there be a conventional track and motor bogie beneath? Certainly has the potential for something very different.