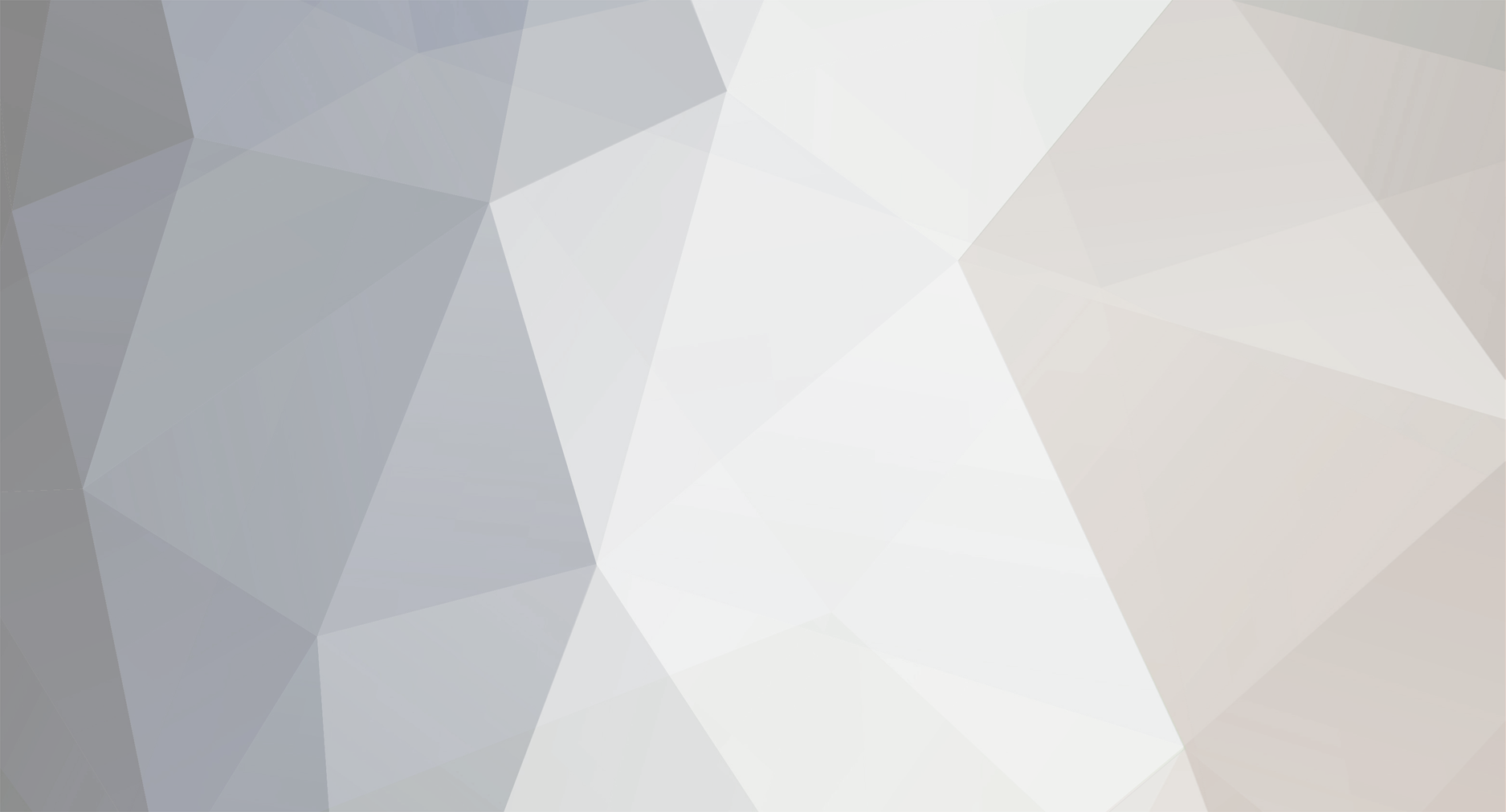
David Holman
Members-
Posts
4,218 -
Joined
-
Last visited
-
Days Won
115
Content Type
Profiles
Forums
Resource Library
Events
Gallery
Blogs
Store
Community Map
Everything posted by David Holman
-
Might be a bit harder to find a chassis and track for that, though it has been done at least once. There was a circular layout at Expo Narrow Gauge a few years back that came over from France based on the Lartigue.
-
Great to see the layout, not least because there is quality everywhere you look.
-
Proper job(s). The camera is indeed a great proof reader to help spot minor errors. Just like text, I fear the eye sees what it wants to see, especially at first, and discrepancies only get noticed later. As for typos, technology doesn't always help either. The cheap and cheerful Amazon tablet I'm doing this on has some very strange ideas about what I type and eighteen months in, I still find myself improving its vocabulary and expending mine on it. Initial problems included 'hooligan' for my surname. Quite liked that, but it has just changed hooligan to Sullivan's for some reason. It also prefers heartache to headteacher, my former job, which could also be described as apt at times. Anyway, great work Ken and will look forward to seeing what comes next.
-
Remarkable photos - many of which could easily grace another book.
-
And another...
- 266 replies
-
- 12
-
-
-
It is either a Sunday, or [as per jhbachill], there are a number of special trains that have just arrived and their locos are on shed for servicing. Either way, a few pictures of the newly installed and bedded in turntable
- 179 replies
-
- 21
-
-
-
Have made the first one public, hopefully and here's the other half of the sequence
- 266 replies
-
- 13
-
-
Damn! Will alter the settings later. However, it is taking about an hour to upload to YouTube. Is there a quicker way? Tried uploading straight to this site, but as well as being slow too, nothing there when it had finished.
-
After a long break, Fintonagh is on the road again next weekend at the Bexhill Show. For those of you who can't get to Sussex, here's a video. Will try to post some more later. https://youtu.be/wbBw9sZIirg
-
Slater's Plasticard do 7mm scale corrugated sheets, so worth checking their website to see if 4mm available.
-
Tasty. Well done Ken.
-
Ye gods, what is the world coming to? Time was, one use a camera to take pictures, nowadays a phone is pretty much all you need to do anything! Truth is, it's amazing what can be done. My first digital camera did everything my previous SLR could do and more. The Nikon Coolpix I use for model photos on this forum cost me fifty quid, yet has 12 mega pixels and does video. Shouldn't be allowed, especially as it can store over a thousand lower resolution pictures on a memory card the size of a postage stamp. Where does it keep it all??? Keep having fun JB, will look forward to seeing what transpires.
-
My pleasure. Good modelling deserves a wider audience. Martyn Welch does just this in his Art of Weathering book.
-
Subtlety personified and no small task either. Ever thought of doing a small photographic diorama? Just a piece of well ballasted and weathered track, like a siding with some surrounding weeds and a photographer backscene. Remove the tension locks and then pose a wagon. Suspect there could be more than a few who will struggle to decide whether it is a model or the real thing, me included.
-
B165 returning light engine is one of my favourites. It really captures the evening gloom.
-
Somebody's having fun! Was trying to decide what it is that makes the layout so effective and then realised it is simple: Space. Rural termini everywhere were pretty much always spread out because land was cheap, unlike a city terminus. Resisting the temptation to fill the baseboard with track, but at the same time having enough length for what looks like a 20 wagon freight is not something you see very often, but certainly works here.
-
I always lay the track across any baseboard joins and cut the rails afterwards. I use screws, rather than nails at the join, so I can adjust their height to the bottom of the rails. Nevertheless, laying curved track across a baseboard joint is always challenging.
-
No idea what this all means, but certainly looks good!!
-
Looks like a nice bit of superelevation there too. What's the radius?
-
At the moment, it is squeak free, but then I always said that was my arm, not the turntable.
-
Fitting the turntable has turned out to be much more challenging that just making it. First I had to prise the old one out, then remove the hand cranked mechanism, so the hole in the baseboard could be increased by around 2cm in diameter. A test fit then showed what I'd feared all along, that the motor gearbox projects about 5cm below the baseboard frames - hardly ideal on a layout that is intended to travel to exhibitions. Spent a fair amount of time pondering on how to manage the electrics too, as controls need to be duplicated to front and rear - and be switchable too. Stuff like this really makes my brain hurt and the number of DPDT switches required was growing exponentially, when I suddenly realised that I could use the hand cranked mechanism instead. This doesn't stick out below the baseboard frames and doesn't required any wiring either, so all that is now needed are a trio of DPDT switches to change the polarity of the deck rails. Fortunately the completed turntable sits at exactly the same rail height as the old one, so that makes life easier. Hence most of the work since has been on painting & weathering, though fitting the running rails required a fair bit of trial and error until I was happy. I've gone for 'weathered concrete for the well, blackened iron for the girders and creosoted wood for the decking. The latter is fairly easy to do, but I find weathered concrete a difficult thing to get right, especially when Humbrol 'new concrete' is a highly improbable cream colour! Thus far, have used a couple of washes of diluted 'metal coat gunmetal' to that, adding weathering powders as I've gone along. Much blending in still to do, as you can see. One other photo is of the F6, now with the correct red background [for the early 1900s] to its numberplate
-
Splendid. Lighting is just one more part of the puzzle. Some photographers like to use artificial light, but when I've had photos done of my stuff for magazine articles [mostly Andrew Burnham, editor at Continental Modeller], he has always used natural light, with long exposures and wide apertures - plus a fancy camera too, of course. The great thing these days is we don't have to wait for photos to be developed, only to find only only one or two were any good out of a roll of 36. The simple act of cropping a digital photo can work wonders.
-
I guess the reason the CDR tends to overshadow the Swilly is that things like livery and architecture are seen as better. Red and cream coaches will outdo grey ones most days, while the Swilly's stations were hardly attractive even on a good day. Add in all the quirky railcars and fine tank engines - plus the fact that the Donegal lasted long enough to be regularly photographed in colour & it is easy to see why the Swilly tends to play second fiddle in many people's minds. If only it had stayed open ten years longer...
-
Fabulous photos of the Swilly. What an extraordinary railway it was.