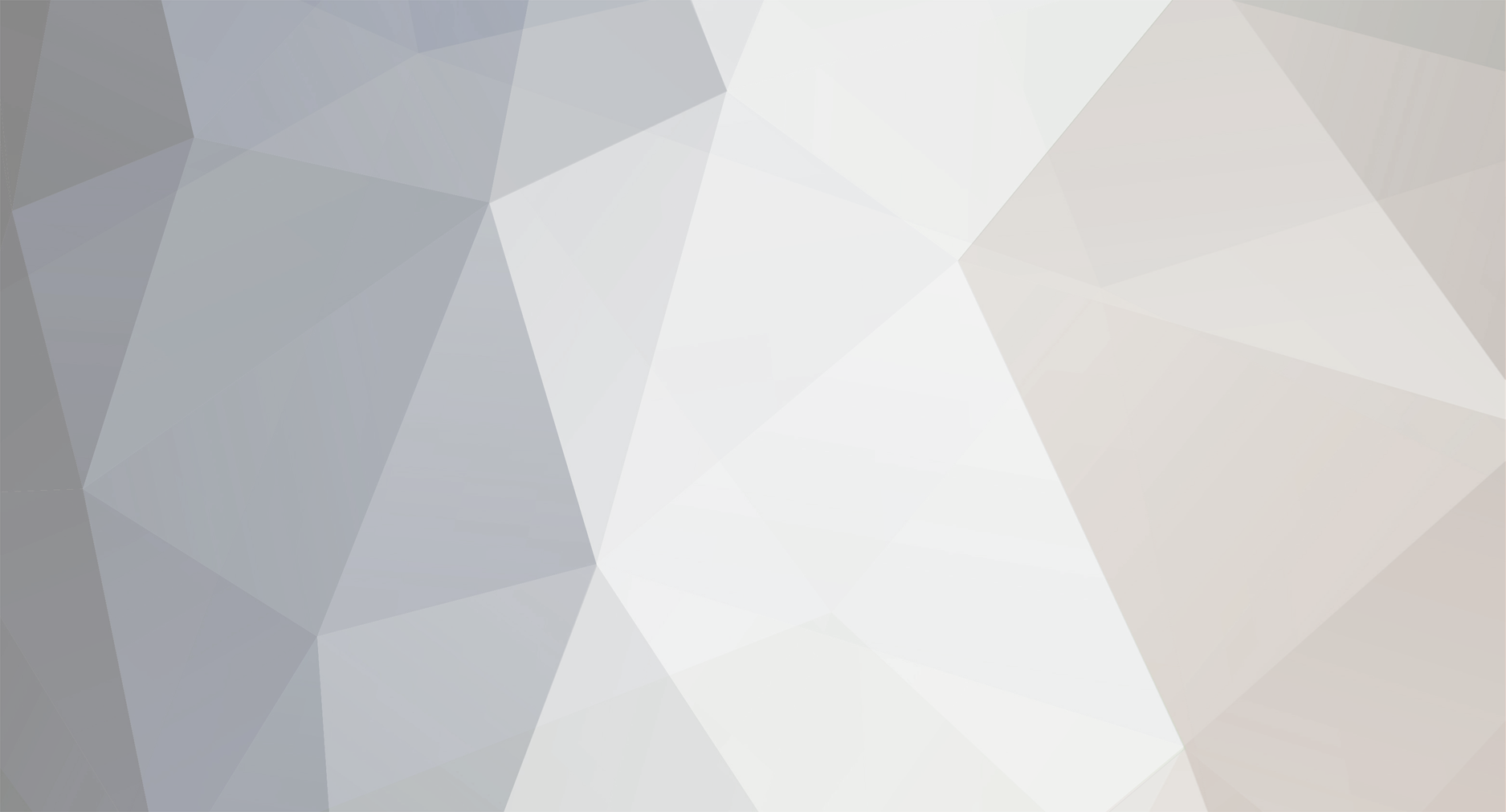
David Holman
Members-
Posts
4,218 -
Joined
-
Last visited
-
Days Won
115
Content Type
Profiles
Forums
Resource Library
Events
Gallery
Blogs
Store
Community Map
Everything posted by David Holman
-
Always interesting to see how folk tackle this type of work. Far from my favourite exercise but somewhat essential... The battery tester is a really neat idea.
-
Spent the last few days fettling the signals, so that both balance arms worked correctly, then added the operating mechanism, which goes below the baseboard. Basically, a piece of 0.8mm wire goes from the other end of the balance levers to pivots soldered below the base plate. Another 0.8mm wire will go from each pivot to a small servo, worked by the Megapoints control panel. This arrangement means the signal can be lifted out for transport, maintenance etc. So, cut a hole in the baseboard surface to enable the unit to sit level with the surface, then set about adding the all important details - in this case the platform [and ladder] for someone to climb up and attend the lamps, plus the finials. After that, it was a clean up and quick spray with primer.
-
Reminds me why I went to 7mm scale! Really fine & delicate work.
-
Brookhall Mill - A GNR(I) Micro Layout
David Holman replied to Patrick Davey's topic in Irish Model Layouts
Here are the two plans I mentioned. The one for Wantage is actually a bit more than 4', but the track plan certainly fits in that foot print. Comes from Rice's book on Light Railways. The second is from his book on Urban Layouts. Like all of Rice's stuff, both are full of inspirational ideas. -
Brookhall Mill - A GNR(I) Micro Layout
David Holman replied to Patrick Davey's topic in Irish Model Layouts
In terms of a prototype for everything, this side of the water, Wantage Town must be one of the smallest footprints of any branch terminus. In 4mm scale, it works out at 1.2m, or four feet in old money. Given this included a covered platform, two loco sheds(!), a loading dock and a kick back siding to the gas works, it was pretty remarkable. Of course, it only ever host four wheel locos, but like anything else could certainly be adapted. My own Fintonagh layout, while 7mm narrow gauge, is only two metres long and the track plan could easily work in 4mm scale. One of the cleverest designs I've seen is by Iain Rice. In 4mm scale, he suggests multiple layout units around 1.2m long and 20-30cm deep. These are arranged on wall brackets, one above the other, fed by a single, cassette type fiddle yard. A train shunts the top layout, exits on to the cassette and is moved down to shunt the next and so on. -
At first, I thought it wouldn't take long to fit the new plates and indeed the first stages were simple - spray black and the once dry sand back to reveal the raised brass figures. After cutting out and filing the edges smooth, the plates were then fixed to double sided tape and could then be stuck on the loco. Nice and easy - however, like the rest of the loco, the cab side number plates were lined in black and white, so out came the Fox transfers sheet again. Unfortunately, I didn't have any of the curves left, apart from some 5'6 diameter circles, meant for driving wheels. Therefore had to do a lot of careful teasing to get these in place around the plates, which was especially difficult on the tighter radii. Once dry, I then used a fine black lining pen to put in the middle line. So, there we are - just about complete now and must say I'm very pleased with the result. Many thanks to everyone who has helped with advice and information, along with all the positive comments which as ever, are very much appreciated.
- 124 replies
-
- 16
-
-
-
Brookhall Mill - A GNR(I) Micro Layout
David Holman replied to Patrick Davey's topic in Irish Model Layouts
Only goes to show how much fun and satisfaction can be had from small projects like this. An example, indeed inspiration, to us all. -
An envelope arrived in the post this morning with a lovely surprise - the name and numberplates I'd ordered from Diane Carney. Definitely looking forward to getting them fitted!
-
Look what I've found... Had another look through Ernie Shepherd's history of the WL&W and on p16 there is what seems to be an early photo showing an 0-4-2T with a brake van. A close up is shown below and it looks not a million miles from the Dublin and Meath brake vans I bought from the Richard Chown estate. Hence have tried to combine the two & a sketch plan is included for comment. The D&M van is 18 feet long on a 10ft wheelbase. Photos in Ernie's book show WLW wagons in unpainted timber, but with black iron work. Was this actually the case, or are the photos done by the builders?
-
Atmosphere! Ballasting going well though you can get away without sawing through it. Rails yes, but gently break the boards apart and the ballast breaks along the grains so when put together again, you get an almost invisible join.
-
No offence DJ, but a lot prettier than the cuboid bus!
-
Jouef HDI for 630 euro landed cost..... is this some kind of joke?
David Holman replied to burnthebox's topic in Irish Models
A few years ago, there was an article about a couple of Dinky toys. The models had never been removed from their boxes, indeed the boxes had never been removed from their packaging! Hence valuation was totally speculative, but inevitably, folk were interested. This highlights the line between collectors who acquire stuff because they like it and those who think they can make money from it, artificially driving prices up and indeed down. Know which side of the fence I prefer. -
Got to be pleased with them!
-
Now that would make a nice model!
-
Many thanks both! Seems to me that brake vans are a sometimes neglected area in early Irish Railway history, but what is available can be fascinating - the MGWR examples especially, though my favourites remain the SLNCR road vans - possibly the shortest mixed train ever? As for the pay coach, the bank counter idea is an excellent one and one wonders if there were ever any Butch and Sundance style attacks, especially in the early years of seeking independence and the civil war too. You'd certainly think there would have to be a safe and the little ensemble must have been a tempting target. Am hoping to get up to Beamish this summer. Meanwhile, need to delve into my photos of Cultra, methinks.
-
Any idea where I might find photos or drawing of Waterford Limerick and Western Railway brake vans? Haven't been able to find anything thus far, but would like to build one to go with my 'mail goods', as hauled by 0-6-0 Shannon. While I'm here, something even more obscure. The new book Locomotives of the GSW has a drawing of Sprite with its 4w coach, which made up the 'pay train'. This toured the whole system on a fortnightly basis, so I fancy having a go at building a model. The question is, what was the internal layout of the coach? Suspect there may have been a toilet at the loco end, but what about the rest? Any ideas welcome, please...
-
That's on my list too...
-
Speaking of pretty engines, Robinson's WL&WR 4-4-0s, which became D15 class were also an elegant design, albeit with only 6' drivers. Featured on the cover of HC Casserley's history, they sported crimson lake livery too and occasionally cross my mind as a loco for Belmullet - but then so do half a dozen others!
-
Made a start yesterday on the two doll signal post. Am using Model Signal Engineering etchings of Saxby and Farmer arms. Have built a few signals over the years and the one word that best sums up the process is - fiddly! I began with the post[s], using a 22ft cast white metal post for the main one and then sawed a second post into sections to make the other. Once assembled with 5 min epoxy, the two posts were drilled through about 2' from the top to take the pivot wire for the arms. The latter are etched in two parts [arm and spectacle plate], which need soldering together with a pivot wire attached. This is then fed through the hole in the post and fixed in place with a small washer on the other side. At the base of the main post two etched brackets are folded up and soldered in place with low melt, then the post is again drilled through for another wire pivot for the operating levers. Thus far, simple enough, but things now get complicated as the operating wires and pivots are added - plus the two lamps. The latter need careful positioning, so they are behind the two spectacle plates when the arms are up/down. The operating wire on the main post is fairly simple - just a matter of getting the length right, but for the subsidiary post [or more correctly 'doll'], which is the bay starter, this needs two pivots to get the operating wire down to the main post. Some railway companies were happy to take a robust operating rod straight down to the ground, but I prefer to route the wire to the base as, like the SLNCR signal, this means the entire unit can be removed for transport - or even to be shared with another layout. The photo shows progress thus far, though I need to rethink the linkage to the second doll as the weighted lever should pull the signal to danger should a wire break, whereas it is actually the other way round at the moment... As for linking the signal up to a couple of servos and the control panel, I may will need a lie down in a darkened room before doing that!
-
Like NIR80, my experience of Tortoise point motors has been excellent. They never seem to go wrong and are easy to set up. The two issues are cost and size, especially depth as they need 10cm baseboard frames to hide them. Having said that, you can fit them sideways with a bit of effort - see my Fintonagh thread in the layouts section. More recently, servos are becoming popular, but you need some sort of electronic control to limit their movement. Cheap to buy though. Basic wire in tube can be very good too and needs no electricity of course.
-
Jouef HDI for 630 euro landed cost..... is this some kind of joke?
David Holman replied to burnthebox's topic in Irish Models
Oh dear... -
You can stop taking the medicine, it's Sir Henry lurking in the background. However, there are problems with the space-time continuum, as it is actually sitting fifty years on the future!
-
Jouef HDI for 630 euro landed cost..... is this some kind of joke?
David Holman replied to burnthebox's topic in Irish Models
Not sure which is worse, the fact that it is wrong, or that somebody is hoping to get 130 quid for it. On reflection though, it has to be the latter. While I wouldn't spend money myself on collecting old model railway stuff, I can see the charm in some of these things and will happi!y spend a few minutes at shows (remember those?) watching Hornby template whizz round in a cloud of ozone. Like most things, gaffs occur and our hobby is not immune - but can't help thinking somebody tried to pull a fast one with a CIE 37 and actually shows the validity of have some sort of 'era labelling' as discussed on another thread. If so, an category now required - fake! -
Along the same lines, a man has the first few bars of Somewhere Over the Rainbow going incessantly through his head, but somehow can't remember the rest. This goes on all day until, very distracted, he steps out into the road and is knockdown by a bus. As he lies there on the ground, the song is still going through his head: Somewhere, over the rainbow, way up high, there's a land that I dreamed of, once in a lullaby... Suddenly, the two tone horn of the approaching ambulance finally jogs his memory: Na na na Na na na... Meanwhile, an Italian rabbit goes into a sandwich bar and asks for a toasted cheese sandwich. Next day he returns and orders a toasted ham sandwich. This goes on for several days, ordering a different one each time. However, at the end of the week he collapsed and is found lying on the floor. When asked what was wrong, he gasped: I mixeda my toasties! Finally, for now, a chicken goes into a library and the assistant is amazed when the chicken actually speaks and says 'Book'. So the assistant gives the chicken a book and off it goes. This happens several times and eventually the assistant decides to follow the chicken to see where it goes. First, it waits at the bus stop and eventually takes a bus going out into the countryside, getting off at the next village. There, by the pond is a frog, surrounded by the books the chicken has brought it. 'Book' says the chicken, placing the new one by the frog. 'Reddit', replies the frog...
-
Thanks Brack & especially for taking time to do the drawing. Must admit I had to look up what a Geneva wheel was/did, but what a clever thing it is! The photo shows my Megapoints control panel. If I'm honest, the system requires more logical thinking than I possess, but is certainly very effective & clever in the right hands. Indeed, though I thought I'd worked out what I needed, I didn't get the specification quite right and now realise that the separate starter for the harbour branch was probably better as a ground signal on the single slip. Meanwhile, I don't have enough ports left in the control panel to add extra switches for the ground signals. I could fit 'Y' connectors so the push buttons for the slip points also operated new servos for the ground signals, but the panel processors control the amount of movement of each servo, so the extra required would only be possible via a lever/bell crank, so it is easier to try and do it straight off the point blades. Unfortunately, the ground signals need to rotate 90 degrees, so I'll need to do some experimenting to see if that is possible. For now, they will have to remain cosmetic.