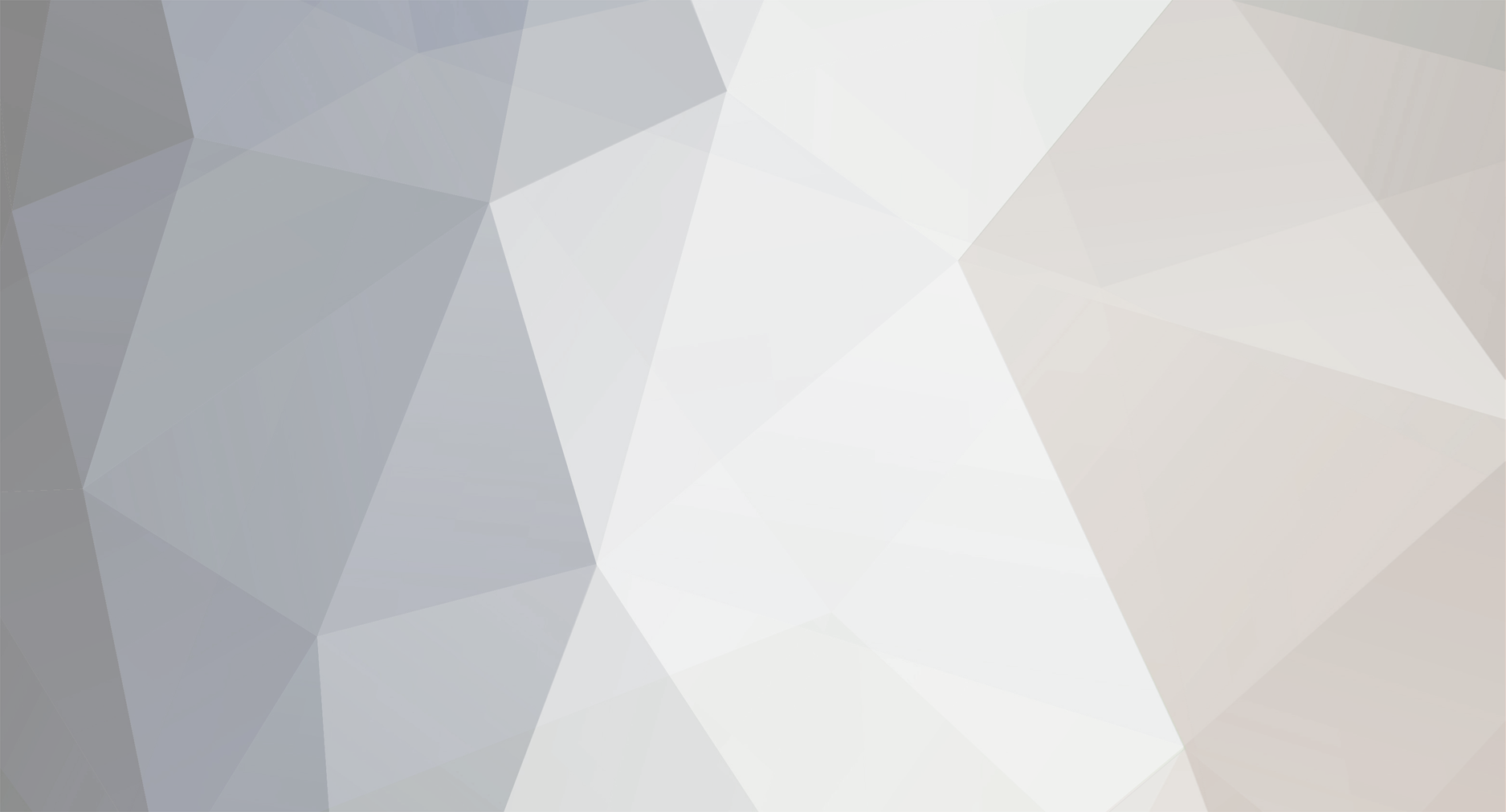
David Holman
Members-
Posts
4,218 -
Joined
-
Last visited
-
Days Won
115
Content Type
Profiles
Forums
Resource Library
Events
Gallery
Blogs
Store
Community Map
Everything posted by David Holman
-
Coming on nicely, Noel. Like the lack of uniformity which is what you get in a station, where brake dust and oil accumulate. The baseboard join is disappearing too.
-
The latest issue has just arrived and is quite a tour de force. Articles on 00n3, converting diesels to 21mm gauge, plus one from Andy Cundick on his C class diesel. Excellent stuff!
-
Believe it or not, the 101 on Belmullet was built from the same etch, blown up to 7mm scale. Amazing to think it was done in three different scales, especially as this was well before the days of CAD. I recorded the build in the workshop thread under the heading 'A tribute to Richard Chown'. Got the kit at Guildex as part of the last remnants of his estate, he's had it since the late 90s and somehow never got round to building it. In 7mm scale, it was fascinating to build, with some clever ideas to ensure the curved footplate goes together well. Guess it is likely the original 4mm etch was photo enlarged to 7mm scale and if so, Terry's work must have been very accurate as the fit of parts was really good, so going down to 2mm should be fine. Putting it together another matter, but it should make an exquisite model. Love the 5p picture. I hand lettered mine with a fine nibbed dipping pen, so this is another level entirely!
-
Progress continues on the WL&WR 'mail goods' train for Shannon. Like most rolling stock scratch builds, you think you've got the model nearly finished, but it is the detailing that takes the time. However, the brake van is now just about there. The first picture shows the plastic shells for both the van and the four wheel coach. The brake van though has been painted, lettered and given a bit of light weathering. The nice thing about both models is that they have been made from what I had in stock, so it feels like they haven't cost me anything. They have, of course - a pair of wagon/coach wheels is around a tenner, couplings a fiver and sets of cast buffers and W irons another fiver each, so £25 is about the minimum for a 7mm scale wagon, plus of course a few hours of [mostly] pleasurable work. The rest of the pictures show the brake van with what will be the rest of its train - all WL&W vehicles, with a six wheel full brake, a carriage truck and a horse box. The latter has been reverse modelled from an SLNCR vehicle I built a few years ago, the prototype actually coming from the WLW. It must be said though that the brake van is decidedly dubious in terms of accuracy, being an amalgam of two early types - Dublin & Meath and Waterford & Central Ireland. I thought about painting it in passenger livery, so that the whole train would be crimson lake, but in the end I didn't have any screw link couplings, so it's ended up dark grey.
-
Wonderful information and can only agree about the horsebox - my 7mm scale one is not as sharp as this.
-
Just been looking back at the 5p pictures to remind myself how tiny these wagons are. Little jewels! The two Dublin and Meath brake vans I got from Richard Chown have their wheel centres in varnished wood,meanwhile, am sure it won't be long before our livery guru can advise. Going back to the horse box, when you think how small it is, the smallest error will throw the shape of it completely, which only goes to show what a fine model it is. Keep 'em coming Angus!
-
Interesting. Using 5.5mm/ft gives a scale of 1:55 - a remarkable bit of symmetry. For comparison: 7mm/0 is 1:43 S is 1:64 00 is 1:72 H0 is 1:87 TT/3mm is (approx 1:100) British N is 1:148 Continental N is 1:160 Without wanting to hijack J-Mo 's thread, I hadn't realised 5.5 was bigger than S. Clearly it was a scale designed to make 16.5mm track work with a known prototype gauge and I believe was also used with 12mm track for two foot gauge. Obviously a scratchbuilders scale, anyone know what figures and road vehicles were used? Another potential Irish scale/gauge combination is 6mm scale. It is close to 1:48, which Americans use for 0 gauge, while 32mm, standard 0 gauge track and 18mm EM, track work nicely for 5'3 and 3'. Indeed has much potential for Irish narrow gauge, with plenty of figures and road vehicles available in 1:48, but works less well with loco driving wheels for 5'3 as scaled down from 7mm, the number of spokes no longer match for a given size. Considered it for a while, but easier to stay in 7mm and use 36.75 track. Anyway, am sure J-Mo's stuff is far more interesting than my wittering here!
-
Excellent stuff, keep posting! One dodge I use a lot on my layouts is a siding going off scene into the fiddle yard. On Belmullet, it is harbour branch, for Fintonagh it leads to a transfer siding for broad gauge, while on Arigna Town it was a branch to the coal mines. The point is that the siding can be anything you want and because it goes off scene, no extra modelling/space is needed, though you have the opportunity to build whatever stock you might want to serve it.
-
Object lessons for us all, add in Ken's similar project and there is much inspiration in these small projects.
-
Excellent ground cover. Presume you used a static grass machine to create the weeds growing through old sleepers and rubbish? Likewise, how do you create the concrete hard standing? Colour and texture look just right.
-
Loco liveries: BCDR & LLSR & MGWR brake van green
David Holman replied to jhb171achill's topic in Irish Models
Remarkable! How long did the Midland vehicles last in these colours? Also, what colour was WL&W freight stock, pre take over by the GSWR? Photos in Ernie Shepherd's book suggest varnished wood with black metalwork, but am guessing that was probably like photographic grey. -
Whatever next?! Having said that Dart Castings have produced a Michael Portillo, in trade mark lurid trousers and a range of scales too, for his railway journeys programmes.
-
With laser scanning and 3D printing, all you need to do is track the lady down and ask her if she is willing to have a model figure made from her. Might be getting on a bit by now though....
-
Indeed! Feel sure a C class will look at home on a Sligo Leitrim layout and never ceases to amaze me on what folk are doing out there.
-
Great work and fine though the modern diesels are, it's lovely to see something different. Will there be some weathering added?
- 64 replies
-
- cbcsr
- cork bandon and south coast railway
-
(and 3 more)
Tagged with:
-
Filling gaps I don't know whether other folk do this, but I often find myself pondering and brooding over the make up of the trains I run on my layouts. For Belmullet in its early 1900s guise, a lot of time has been spent recently on the MGWR Mail Train, which is now finished. There are seven tracks in the fiddle yard and there have been more than a few furrowed brows over the last few months about how I might fill them. Some were fairly easy, such as a Sligo Leitrim freight, hauled by 'Small Tank' Fermanagh. This is made up of SLNCR cattle wagons, or private owner coal wagons from the Arigna mines, so that's three roads done. A fourth road is occupied by a Waterford, Limerick and Western 'Mail Goods', with 0-6-0 Shannon at the head, with a 6w parcels van, 4w carriage truck and horse box from the same company.. However, have only recently realised that I only had two passenger trains, so have decided to turn the Mail Goods into a mixed train, by adding a 4w third class coach - more of which later. The fifth road was originally occupied by my Coey 101 class 0-6-0, but have recently decided to put this loco on freight duty - which is where a few more gaps need filling. Currently, I only have one GSWR van, plus a brake, so a couple more need adding to the stock building list. At least one open topped livestock van, plus an open or two are currently favourite. As for the GSWR passenger, this comprises two six wheelers & have decided I would now like them to be hauled by an F6 2-4-2T. These were really built for the Valencia Harbour line, but [had it been built] the Belmullet route would have been similarly twisty, so an F6 moving north is not out of the question, while Galteemore of course has one on Rosses Point! Alphagraphix do a kit though it will need adapting to its original [oven type] smokebox doors. A couple of fish vans would complete things nicely. So that is six roads covered. The seventh is split in two, with in 1950s guise the railbus at one end and the railcar at the other. For the 1900s, the short [railbus] end will eventually be occupied by 0-4-2T Sprite and its semi permanently attached pay coach. In the longer road, there is room for a short goods train and news that Alphagraphix are due to re-release the E/J26 kit offers the chance of doing a MGWR goods, with the loco in lined green too. I quite like the idea of having each of the independent railway companies operating their own trains & stock. This side of the water, wagons in particular eventually all got mixed up, so that by the 1923 grouping, you could find a variety in most trains. Suspect it was the same in Ireland, so the GSWR freight, hauled by the 101, will have a variety, but the WL&W, MGW and SLNC ones will stay 'independent'. Among the stock I've built, this is not a problem, but having acquired two Richard Chown Dublin & Meath brake vans, I've wondered ever since how to include them. These are the ones in purple lake with salmon pink ends [!]. Richard ran them with Shannon on the Mail Goods, but the Dublin & Meath was taken over by the MGWR, so by 1900 should I suspect, be in brown livery. So, one at least can be repainted as the brake for the MGW freight, plus I have a horse box from the same company. A couple more MGW wagons should complete the line up. So, where does all this lead - and apologies if you are now bored to tears with my ramblings! The latest mini project centres on the WL&WR Mail Goods. In Ernie Shepherd's history, there is a nice picture of a four wheel third class coach which [unlike the parcels van] has plain panelling and doesn't need an awkward lattice cutting out, so can all be done with micro strip. Alongside this, am building a Waterford and Central Ireland Railway brake van. This company was actually in open conflict with the WLW for a while, over access to Waterford station, but later the former took over working its trains for a few years, before the WCIR became independent again. In the end, it was absorbed by the GSWR, so am hoping my model is vaguely plausible. One thing for sure, early brake vans are not easy to find, so this one is a bit of an amalgam of the WCIR and D&M prototypes. However, the rounded tops to the panelling nicely match those of the 4w coach, so fingers crossed! The models very much follow techniques used by David Jenkinson in his book Carriage Modelling Made Easy. Plastic sheet and micro strip make up the bodywork for both, while the spares box seems to have enough white metal castings for W-irons, springs, buffers etc. Deciding how my trains will be made up may cause a bit of head scratching, but if you can make stuff yourself, at least you don't have to wait for a manufacturer to produce one.
-
Excellent work - well done you. There is probably more fun in building modules like this than actually operating them, but as your pictures show, they are great for posing and photographing models. Plus of course, one delvelops new skills in the process and the project gets going pretty quickly too.
-
Diesels, yes, but steam locos more challenging because of splashers and bodywork outside the wheels, meaning a lot of hacking and rebuilding needed. The actual NCC Jinties ad to have their drivers reprofiled to fit inside the splashers when they crossed over the water. An ideal loco for simple conversion would be one where the footplate was clear of the drivers and with inside cylinders and valve gear. Not many of those around, I suspect, with even fewer available as ready to run models...
-
Well ahead of its time. Could be driven from either end and had sliding doors, albeit not mechanical. The railbus meanwhile had Howden-Meredith patent wheels, where the steel, flanged railway tyre was fitted outside the conventional rubber ones, in an effort to improve the ride. Even had pressure sensors that sounded a hooter in the cab if any of them started to go flat. Now a standard feature on most modern cars of course, but Dundalk works thought of it about 90 years ago.
-
Alchemy going on here, methinks! Sounds like you should put all the stuff back in a box for a few days and see what else appears - maybe a motor or two???
-
Agreed! I think most people who build their own stuff are happy to plan ahead and/or wait a bit. That said, Alphagraphix normally only take a week (probably for cheques to clear), while the likes of Eileens Emporium, Roxey Mouldings and Wizard Models turn things around very quickly and you can use credit card or PayPal. Collectively they have certainly helped me through lockdowns, but also very much looking forward to proper shopping again at shows. My local model shop had no microstrip whatsoever when I visited this morning, so an order to Eileens is now required for the next project.
-
Wow, well done Roger. Not before time we might say, especially as I only recently sent the usual 6x second class stamps for the paper version! Given there are a few photos of my models in there, goes without saying am a long time fan of all things Alphagraphix. As Galteemore says, the card kits work well on their own and you can add a whitemetal chassis too, though I prefer to use them as drawings for scratch builds from plastic. Not only can you do West Cork, you can also do most of the Sligo Leitrim as the card kits cover box and cattle wagons, along with most of the coaches AND the railbus, plus many of the railway buildings too. Note though my model of the railbus is made of plastic and nickel silver - indeed would think this is easier than trying to bend card into all those complex shapes. Couldn't have done it without the card kit though and the whole catalogue is a fantastic resource, because there are whitemetal castings for bits and bobs, transfers and all sorts. Arigna Town was largely built from it. The loco kits are great too, because the chassis is a very simple, one piece etch. Solder in the wheel bearings (facing outwards for 5'3), fold up the frame sides and fold down the spacers, then they presto, you have a chassis! On an 0-6-0 I've had wheels and rods on in about an hour - very satisfying. Roger has some clever tricks for dealing with complex shapes like curved footplates and would say that many of the kits are well within the scope of an enthusiastic beginner and likewise the coaches too. Only St Mologa was a bit of a challenge, but even then more because of its tiny size than anything. If there aren't a few more folk (and should be a lot more!) modelling Irish broad gauge in 7mm scale as a result of the catalogue going online, then there is no justice. Come on in - the water is lovely!
-
Signals may be fiddly, frustrating things to build [for me anyway], but they are a delight to finish off because they transform with only the minimum of painting. In this case, a coat of matt black from a spray can, then I hand painted the white bits, then added the red and white stripes to the front of the arms with black and white to the rear. Next came red and blue [not green, yellow light from the lamp turns blue green] gels to the spectacles, with some textured cement coloured paint for the base. The operating mechanism is yet to be fixed up, indeed it is something I'll need to psyche myself up for, involving as it does separating the boards and lifting No2 up to get at the underside to fix the servos. However, Belmullet at least now has an almost complete set of signals, though have just noticed that the point to the end loading dock ought to have a ground signal too.
-
Goes without saying that Mayner knows his stuff! One thought to get you started would be doing Phoenix. Worsley do a set of etchings that are pretty much self explanatory and it ought to be possible to source a 4 wheel motor bogie to go underneath it. That way you could have something up and running to go with any stock you make and Phoenix was known to go on short forays along the main line from time to time. Small shunting layouts have been built around less and could always be incorporated into a larger scheme later.
-
Although I've not direct experience of Backwood kits, from what I hear they are quite complex and not cheap either, but then there is a reason for this as Donegal steam locos were fairly complex things too. Outside frames and cranks, outside cylinders, bogie and pony trucks - there are a lot of skills to learn and indeed tools to acquire for anyone wanting to build a model of these locos. That said, the big side tanks will help hiding the motor gearbox. I have built a few Worsley Works items and the thing with them is they are designed as an aid to scratchbuilding. So, as you say, not only no wheels, motor or gears, but no castings or fittings either. What you get are a set of etched and that's it. There are no instructions to help you assemble the model. Would say that trying a couple of wagons is certainly a good way to start. A good way of getting into loco building can be to use/adapt a commercial chassis and scratchbuild the body, which plasticard can be great for. However, not sure if there are any 12mm gauge, outside frames chassis available that might suit. Definitely think you are right to use 12mm track though. Donegal locos are way too big for 9mm. The same applies if you went to 7mm scale. There are chassis that could be used, notably the 08 shunter, which runs beautifully. Then there is 6mm (quarter inch) scale on 18mm track, but suspect I'm now way off piste! However, certainly applaud the idea of wanting to try something more demanding and will certainly look forward to seeing how things develop.